300MW汽轮机高压主汽阀阀杆断裂原因分析
通过化学成分分析、断口分析、金相分析、电子显微分析和能谱分析,确定了某300MW汽轮机1号高压主汽阀阀杆断裂的原因,为错用了25Cr2MoVCu钢,而非设计的2Cr12NiMoWV钢所致。过高的淬火温度造成组织粗大,晶粒度达到4级,且存在富铜相、带状组织和大量夹杂物,使钢产生较大脆性。在淬火过程中,组织应力和热应力使弹簧内孔根部产生应力集中,致使形成淬火裂纹,阀杆启闭产生的应力使裂纹扩展,最终引起阀杆断裂。
某电厂300MW亚临界燃煤发电机组型号为M300-16.7/538/538,额定主汽压力为16.67MPa,额定主汽温度为538℃,累计运行20566h后,在第一次A级检修后的开机过程中,发现2号高压阀门在带高负荷时波动较大,一侧高压配汽机构的1、3、5号高压导管压力异常。对1号高压主汽阀和其后部所连接的1、3、5号高压调速汽阀进行带负荷试验,发现负荷没有变化,据此推断认为,1号高压主汽阀阀芯可能出现开关故障。停机后对1号高压主汽阀进行解体检查,发现阀杆在应力集中的预启阀部位发生了断裂,并在同一断裂层含有新旧两部分断痕。为分析确定该主蒸汽阀阀杆断裂的原因,进行了化学成分分析、断口分析、金相分析、电子显微分析和能谱分析。
1、化学成分测定
生产制造厂家提供的设计图纸标明,该阀杆材料为2Cr12NiMoWV马氏体不锈钢,热处理制度为调质。2Cr12NiMoWV钢是强化的12%Cr型马氏体耐热不锈钢,其合金元素Cr、W、Mo含量略高,缺口敏感性小,具有良好的减震性和抗松弛性,综合性能较好,国标GB/T20878—2007《不锈钢和耐热钢牌号及化学成分》要求的化学成分见表1所列。从主蒸汽阀阀杆端部割取试样进行化学成分分析,其化学成分测定结果见表1所列。
阀杆的化学成分(质量分数,%)

对比表1的数据发现,阀杆的实际化学成分与2Cr12NiMoWV钢(国标GB/T20878—2007)的化学成分完全不符,其主加元素Cr的含量仅为1.62%,远远低于国标要求的11%~13%,Si、Mn、Ni、Mo、V、W含量均低于国标要求,而且,有0.14%的Cu元素,而2Cr12NiMoWV钢中不含Cu元素。根据化学成分分析结果判断,该阀杆用钢仅相当于25Cr2MoVCu钢,并不是2Cr12NiMoWV钢,因此,该阀杆属于错用钢材。
2、断裂阀杆的断口特征
2.1、断口的宏观特征
阀杆断裂发生于预启阀部位,断口位于阀杆的变径处和弹簧内孔根部处,如图1。在断口附近切割取样后,发现在弹簧内孔根部处有多条裂纹,如图2(a)。从裂纹及断裂特征看,裂纹及断裂位于阀杆变径处和内孔根部的应力集中部位。断口如图2(b),具有以下宏观特征:
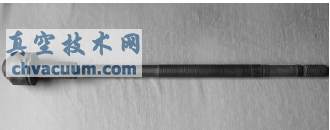
图1 断裂后的阀杆
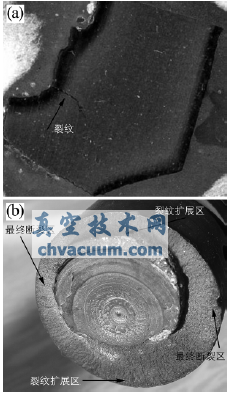
图2 弹簧内孔根部裂纹(a)及阀杆断口的宏观形貌(b)
1)断口为粗糙颗粒状,无明显塑性变形,属脆性断裂。
2)断口有明显的四个区域,两个区域具有明显的氧化和腐蚀现象,呈暗红色,说明裂纹早已形成,在运行中不断扩展,不断被氧化和腐蚀。另外有两个白亮区,属最终断裂区。暗红区域要大于白亮区域,说明裂纹扩展过程所受应力不是很大,属于缓慢扩展过程。
3)断面上有台阶。台阶是变径处表面裂纹在向内扩展过程中与弹簧内孔根部裂纹产生扩展连通造成的,说明断裂过程中,既有变径处表面形成裂纹并扩展,又有弹簧内孔根部裂纹的扩展。
由图2(a)可以看出,弹簧内孔根部处圆弧过渡不光滑,过渡半径R值偏小,微裂纹起源于此处。圆弧过渡偏小会产生应力集中,是产生开裂的一个原因。
2.2、断口微观分析
在扫描电镜下对断口进行观察,结果如图3,(a)~(c)为不同倍数下的断口形貌特征,(d)为扫描电镜背散射形貌特征。由图3(a)~(c)可见,断口上有明显的氧化物附着,这是由于阀杆断裂后,经受了一定时间的高温高压水蒸汽氧化所造成。但是,即使有氧化物,也依然显示出显著的冰糖状特征,表现出典型的沿晶断裂特征。由断口的微观形貌特征断定,该阀杆的断裂为沿晶脆性断裂。图3(d)的扫描电镜背散射显示,基体中有大量块状白亮相。对块状白亮相进行电子探针测定,发现该相为富Cu相,Cu含量高达15%以上,如表3所列,如图4所示。铜在钢中溶解度极小,通常以游离聚集态存在,显著增加钢的脆性,特别是以块状形态存在时,极易引起脆性断裂。
3、金相组织分析
从断口部位取样进行金相组织观察分析,结果见图5。结果显示,①该阀杆的金相组织为板条马氏体组织+少量粒状贝氏体,晶粒度评级为4级,晶粒粗大,如图5(a)。②存在带状组织。带状组织是在轧制过程中形成的,在调质之前若没有进行正火处理,在调质后会依然保留。存在带状组织说明,该阀杆的热处理工艺亦存在缺陷,如图5(b)。③钢中存在大量夹杂物,呈带状分布,如图5(c),说明该阀杆存在冶金质量问题。在进行金相组织观察时,发现多条微裂纹,见图6(a)、(b)。各条裂纹均位于圆弧角应力集中部位,起源于表面,向基体扩展,呈现显著的沿晶扩展特征。这说明,该弹簧内孔根部裂纹应产生于淬火过程中,而不是运行过程中。
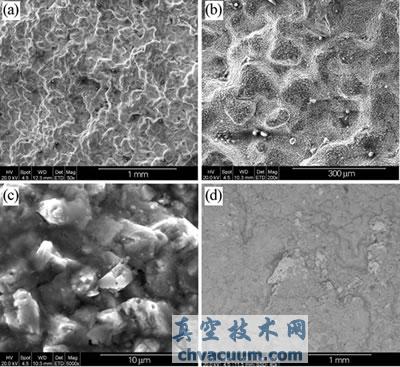
图3 断口的扫描电镜形貌
(a~c)扫描电镜照片;(d)背散射形貌特征
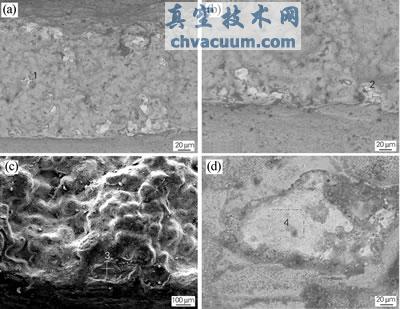
图4 阀杆断口处的富铜相
表3 断口能谱分析结果

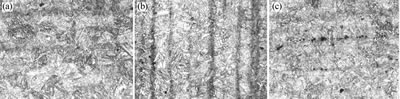
图5 断裂阀杆基体金相组织 ×100
(a)基体组织;(b)带状组织;(c)夹杂物
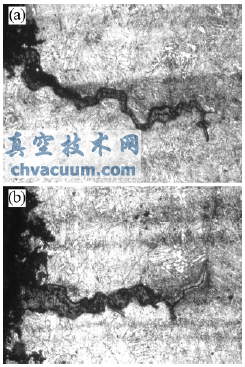
图6 阀杆断裂部位的裂纹 ×100
4、断裂原因分析
根据化学成分分析结果可知,该阀杆选用的钢材仅相当于20Cr2MoVCu钢,并非2Cr12NiMoWV钢,属于错用钢材。2Cr12NiMoWV钢的淬火温度为1020~1070℃,而根据含碳量及Cr含量估算,该阀杆用钢(相当于20Cr2MoVCu钢)的淬火温度仅为840~860℃,如果在1020~1070℃淬火,晶粒会显著粗化,得到粗晶组织,脆性增加。在淬火时,由于较大的组织应力和热应力,在应力集中的部位很容易导致淬火裂纹。该阀杆的外侧变径处和弹簧内孔根部,均易引起应力集中,而且还存在带状组织、含有大量夹杂物和富铜相、弹簧内孔根部过渡圆弧R值偏小等缺陷,因此,在淬火过程中,组织应力和热应力引起了弹簧内孔根部的沿晶开裂,形成多条裂纹。在运行过程中,阀门启闭时会产生一定的应力,并在阀杆变径处产生一定的应力集中。由于阀杆为粗晶及带状组织,并存在大量带状分布的夹杂物和块状富铜相,导致了基体极大的脆性。这种情况下,应力集中足以使阀杆在外侧变径处表面产生裂纹。阀门不断启闭产生的应力,促进裂纹的不断扩展。当裂纹扩展到与弹簧内孔根部的裂纹接近时,就产生连通,形成台阶,最终导致断裂。在裂纹扩展过程中,一直伴随有高温高压水蒸汽氧化,使断口产生氧化,形成大量氧化物。
5 、结论
1)该阀杆用钢仅相当于20Cr2iMoVCu钢,并非设计要求的2Cr12NiMoWV钢,属于错用钢材。
2)该钢基体组织为板条马氏体组织+少量粒状贝氏体,晶粒度为4级,晶粒粗大,且含有大量富铜相,存在带状组织和大量夹杂物,存在冶金质量问题。
3)弹簧内孔根部过渡圆弧R值偏小,且不平整,引起较大应力集中。
4)弹簧内孔根部的裂纹是淬火裂纹,属工艺裂纹,是由于淬火温度过高造成晶粒粗大并产生脆性和应力集中所致。