锅炉减温减压控制系统的改造与实现
基于对锅炉减温减压控制系统不稳定的原因分析,从控制系统的硬件和软件两个方面,对容易损坏的部分进行技术性变革。整个系统结构简单,提高了控制系统的可靠性,最大限度地减少系统故障,对安全、高效生产有现实意义。
工艺参数的稳定可靠是保证产品质量的重要前提。某轮胎公司目前半钢产量约为15000套/天,半钢生产过程硫化工艺所需内压蒸汽的连续供给,平常是由动力厂热电站汽轮机一级抽汽得到,而在汽轮机不能正常运行时,由双减系统将锅炉出口过热蒸汽经减温减压后对外供汽。由于执行机构工作环境恶劣,系统干扰因素太多,容易引发控制失灵,最终导致工艺参数超标。而这种故障发生具有突发性和危害性大的特点,因此,如何改善双减系统控制品质,消除控制系统故障,使其运行可靠,成为设备改造的重点课题。
1、减温减压控制系统缺陷分析
目前双减控制系统工作的模式是:锅炉供给压力为3.2~3.6MPA、温度为420℃~445℃的过热蒸汽,经双减调节阀减温减压后成为压力在1.47~1.52Mpa、温度在230℃~240℃范围的外供蒸汽,其压力和温度控制是由传感器测量压力、温度信号后经配电器进S9000控制器,由控制器发出控制信号通过手操器对现场调节阀进行控制。
针对可能导致控制系统不稳定的各环节的现场深入分析:现场环境温度长期高达60多度,电子元件容易老化;信号传输路线长,经过发电机、配电室等强电区域,容易产生干扰信号;同时调节阀工作前后压差大,使用时间年久,导致阀门卡涩、泄漏量大、动作不灵敏甚至误动作等。多种因素将导致经常出现系统控制失灵,轻者半钢硫化车间出现成批废次品,严重时不得不停产。
2、减温减压控制系统的技术改造与实现
根据对双减控制系统不稳定的原因分析,我们将容易损坏的部分进行技术性变革,提高双减装置的工作效率,确保锅炉安全、经济、稳定运行。
2.1、更换新型配电器
原配电器电路设计不合理,联结部份采用焊接结构,容易产生接触不良;电子元件温度漂移使得准确度下降,针对这种情况,我们重新选购了电路设计合理、便于维修更换(插拔式)能够减少维修时间的新型号配电器,同时将配电器、压力变送器的校验周期由原来一年一次改为2个月一次,保证了参数测量的精确度。
2.2、改进联轴器结构
原电动执行机构生产厂家设计的联轴器是整体式,且固定螺栓只有2个,丝牙容易损坏,而一旦丝牙损坏更换非常麻烦;经过重新测量尺寸绘图加工后,改为由两块组成,将联轴器的固定螺栓由2个增加为4个,外加并帽,并定期检查固定螺栓松紧程度。
2.3、环境温度高及强电干扰的应对措施
由于现场环境恶劣,环境温度高,特别是夏季,可达到60多度,几乎工作在仪表技术参数的极限范围(-25℃~70℃)电子元件长期工作与此环境下,极易老化,从而稳定性急剧下降;另外我们发现伺服电机的绝缘性能也已下降,极易烧毁。对此,我们仔细测试了现场仪表上的每个电子元件的性能,对于技术参数指标有所偏差可能的不良元件全部予以了更换;对伺服电机,将相关技术参数提供给马达组由其重新绕制,经装配、接线、调试运行试验证明完全可以代替使用;传输信号经过发电机和配电室等强电区域,易产生干扰信号,我们对系统每个环节进行了逐一检查,改变了局部电缆走向,将不是屏蔽的电缆改为屏蔽电缆,并保证接地牢靠。
2.4、对控制系统失灵的改进
双减控制系统的工作原理是:压力控制是由压力变送器检测压力信号后经配电器进S9000控制器,由S9000控制器发出控制信号通过手操器和执行机构反馈来的阀门位置反馈信号进行运算后,直接输出正反转信号驱动电动执行机构电机,控制电机正反转,而电机正反转动作带动调节阀阀杆上下运动,从而改变蒸汽阀门开度,起到调节压力作用;值得一提的是,此调节阀与一般调节阀结构不同,阀门底部加入减温水在阀门内与蒸汽混合,其减温水量由减温调节阀出口控制。其温度、压力控制原理图如图1所示。
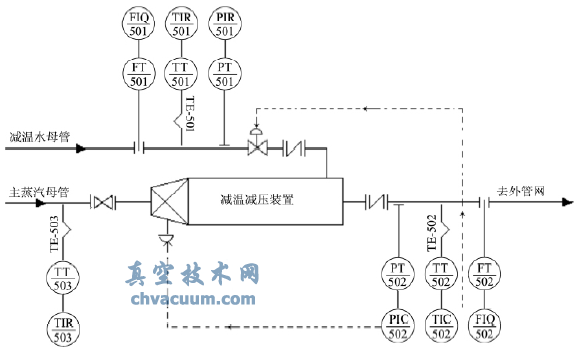
图1 双减温度、压力控制系统图
双减温度、压力控制原理方框图如图2所示。由于阀门前后压差大,用户负荷变化不定,用人工调节难以达到工艺指标。为了保证核心部件控制器可靠性,我们进行了下列几方面的改造:
①将易导致故障的逻辑处理器Run/Disable钥匙转换开关改成跳线转换;②将与上位机通讯的接头固定牢靠;③为了以防万一,决定增加一套后备自动调节系统。即增加两台单回路智能调节器和两个转换开关,改变系统接线方式,当S9000控制失灵时切换转换开关,投入智能调节器控制。改造后控制系统图示如图3所示。
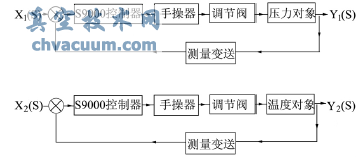
图2 双减温度、压力控制原理方框
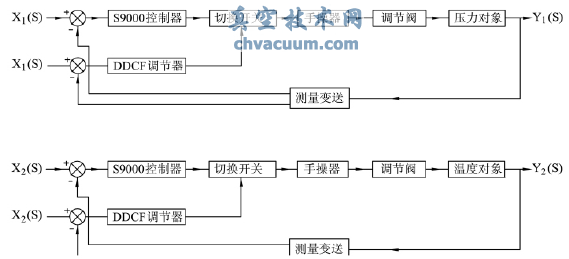
图3 改造后的双减温度、压力控制原理方框图
2.5、调整电动执行机构
对电动执行机构进行拆检,我们发现涡轮涡杆机构滚珠行程轨道不光滑,部分滚珠磨损严重,更换所有的滚珠,打磨不平轨道,改用耐高温的锂基脂作为转动部件润滑油;对阀门和电动执行机构进行重新组装,保证既能满足工艺需要,又能符合调节要求,合理调整刹车机构松紧程度;改变手操器的设定参数,不断修正执行机构动作灵敏度,使其既能不可能发生卡涩又不易造成振荡而失控现象。
2.6、重新整定控制参数
根据自动控制理论,由于压力测点装在减压阀后不远的地方,压力变化时反应较快,即压力调节对象的滞后时间很小,上升速度很快,因此,整定调节参数时,放大倍数应设置得大一些,积分时间小一些,由于微分作用对快速调节对象的反应敏感,一般不采用微分作用,理论要求放大倍数K=2.5~5,积分时间Ti=5~10秒;而减温通过减温水来控制,温度测点离喷水点距离较近,K=2.5~5之间,Ti=10~20秒,Td=(1/2~1/3)Ti,由于压力变化对温度影响较大,投好压力自动调节有利于温度控制质量的提高。根据这一理论的指导,结合我们的实际工况,经过我们几个班次跟踪设备的运行,不断摸索,终于得到最佳的的PID控制参数,使得系统不仅控制及时、而且无振荡,压力和温度精度得到提高。
2.7、调整运行工作方式
由于阀门长期使用后有一定的泄漏量,使得在低负荷时阀门工作特性较差,从而影响控制质量,此时我们要求运行人员合理地开大另一台双减调节阀,以增大该双减调节阀的负荷,(另一台双减调节阀安装在该双减调节阀后,是后者的一个分支,提供9公斤蒸汽,此蒸汽通常由发电机背压排汽得到,若另一台双减调节阀开得太大,势必影响发电机发电量,这样就不能达到经济运行),实践证明,此项措施非常有效。
3、小结
经过对双减控制系统的改进与反复调试,生产自动过程得以实现,从改造后近两年的运行情况看,生产效率明显提高,极大地提高了锅炉蒸汽供给系统的稳定性和可靠性,具有显著的特色和很大的实用价值。至今的生产运行状况来看,已取得了显著效益:
(1)此改造项目,总投资约5000元人民币,主要用于购买4台单回路PID调节器、配电器、部分电子元件等,其余材料均就地取材,减少了投资,节约了维修费用。
(2)彻底消除了阀门的卡涩,排除了因阀门的不正常开关给锅炉和压力管道带来的安全隐患。
(3)改造后,未出现因设备故障而导致工艺参数超标、半钢车间因此而出现废次品,更未因此而停产,保障了正常连续生产。