基于FLUENT的节流管式调节阀结构优化
应用三维建模软件Pro/ENGINEER对节流管式调节阀进行了实体建模,抽取阀门内部流道,采用前处理软件ICEM-CFD划分流道的计算网格。应用计算流体力学软件FLUENT对阀门流道进行三维数值模拟,得到节流管端面处的压力分布,并通过二次计算得出阀门电机功率。在此基础上,对阀门流道进行优化,通过对比分析不同流道对应的阀门电机功耗,得到了更为理想的节流管式调节阀结构尺寸。
调节阀是流体输送系统中重要的控制部件,广泛应用于核电领域。核动力装置对调节阀的性能要求都很高,不仅要确保调节品质,还需要降低阀门功耗。节流管式调节阀是哈尔滨工程大学研制的一种新型调节阀,用于流体输送管道的流体压力或流量的调节,特别适用于核动力装置各回路系统。它采用自身的高压流体作为工质,通过调整节流管端面与活塞中心处的轴向泄流孔端面之间的间隙来改变活塞两侧受控流体的压差,进而使与活塞联动的阀盘移动并精确平衡在所要求的位置上。
近年来,随着计算机和计算流体力学(CFD)的发展,数值模拟的优越性越来越明显,已经开始用于研究流体机械的内部流动。节流管式调节阀的内部结构比较复杂,本文运用CFD软件FLUENT对其内部流场进行了三维数值模拟,并详细研究了不同阀门结构的内部流场受力情况和阀门驱动电机功耗。
1、节流管式调节阀结构及三维建模
本文应用三维建模软件Pro/ENGINEER建立流道模型。
1.1、建立流道模型
图1是节流管式调节阀的结构图。它由阀体、阀盘组件、活塞组件、节流管组件、双面法兰以及阀门外围部件构成,流体从右侧流入,左侧流出。阀门公称通径为DN80/100,设计压力为4.2MPa,工作压力为(2.15±0.10)MPa,减压压力不低于0.5MPa。
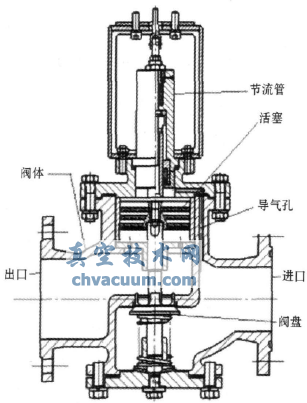
图1 节流管式调节阀结构图
从图1可以看出,节流管式调节阀内部的流道比较复杂,若直接对流道进行建模将面临很大困难。本文首先建立阀门的实际模型,然后建立一个内部无流道、但外部结构尺寸和实际模型一样的“实心体模型”,最后将两者重合装配为一个组件,对重合的阀门组件依次采取“编辑”、“元件操作”、“切除”操作,即得到阀门流道模型。为了减少计算量和节约计算机资源,对节流管内部上半部分的流道做简化处理,并采用流道的一半为计算区域,图2为抽取出来的流道模型。
1.2、划分计算网格
利用专业的前处理软件ICEM-CFD对流道进行网格划分,由于流道复杂,采用的是非结构化的四面体网格。阀头附近流体的速度与压强的梯度很大,对此区域进行网格加密。流道网格划分如图3所示,节流管式调节阀开度为30%,网格数量为79万。
2、模拟计算及结构优化
本算例采用计算流体力学软件FLUENT对调节阀流场进行数值模拟。
2.1、边界设置
启动FLUENT,选用三维双精度求解器,导入流道网格。采用三维稳态隐性压力基求解模型,湍流模型选用k-ε湍流模型;流体介质采用水,作不可压缩流体考虑,设置重力加速度为-9.8m/s2;湍流强度取3%,设置进口面边界为压力进口(2MPa),入口水力直径为0.08m,出口面边界为压力出口(1MPa),出口水力直径为0.1m;采用SIMPLE算法和一阶迎风离散格式,残差精度设为10-5,并监控出口面的流量变化。
2.2、节流管组件机械传动计算
节流管式调节阀的执行器机构是一个小功率电机,其最大功率为25W,工作电压220V,电机设计参数为15r/min。螺杆的螺纹是普通三角形螺纹,其公称直径为d=8mm,螺距为1.25mm,中径为d2=7.188mm。
螺套管每分钟向下运动L=15×1.25=18.75mm;
螺套管运动速度为:


螺杆和螺母的材料均为钢,查得螺纹副的摩擦系数f=0.17;
螺纹当量摩擦角ρ',其正切值为:

螺纹升角ψ是螺旋线的切线与垂直于螺纹轴线的平面的夹角,其正切值为:

在螺杆和螺套管之间存在螺旋传动,该螺纹副的传动效率为:
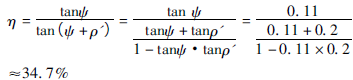
假定电机的工作效率为100%,电机沿竖直轴线转动,通过螺杆传动向下的作用力。电机每转动一周,螺杆也转动一周,螺套管向下运动一个螺距的位移。设P为电机功率,P'为电机传递到的螺套管直线运动时的功率,而考虑螺纹副的传动效率,其对应的转化关系可以根据公称直径与螺距的关系(如图4)得出:
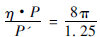
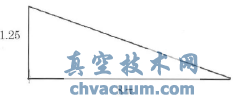
图4 公称直径与螺距的三角关系
根据功率、速度与力的关系:

电机带动节流管向下匀速运动,由牛顿第二定律可知其作用力F'等于流体对节流管的压力F,即
F'=F (3)
则电机消耗的功率P为:

其中:a≈0.0181m/s。
2.3、结构优化
通过上一小节的机械传动计算可知电机功率和节流管压力成正比,本文就是从减少节流管所受压力的角度对流道进行优化设计的。通过观察流道结构,可以通过减小阀体中的导气孔直径来减少阀门电机功耗(导气孔结构如图2所示)。
节流管式调节阀阀体中的导气孔实际直径为6mm,应用Pro/E软件改变节流管式调节阀中导气孔直径,将直径分别改为4、5、7、8mm,并抽取各流道模型 ,划分网格,导入到FLUENT里进行数值模拟。表1为计算得出的节流管所受轴向压力以及活塞的受力情况。
表1 改变阀体中导气管直径时节流管的受力

通过式(4)可计算出当导气孔直径为4、5、6、7、8mm时,所对应的电机功率分别为2.39、2.49、2.65、2.836、3.02W。
从图5中可以看到,当减小导气孔直径时,活塞上表面的压力也随之减小,活塞两侧流体的压差也减小。活塞是带动阀杆向下运动的主要动力,若过度减小导气孔直径,会影响到活塞的合力,进而影响阀门开启。因此,适当的减小阀体中的导气孔直径,可有效节省阀门电机功耗。图6为电机功率随导气孔直径变化的曲线图,从图6中可以看到,改变调节阀阀体中的导气孔直径后,电机功率随导气孔直径的变化很明显。当导气孔直径大于阀门实际直径时,电机功率随着导气孔直径的增大而增大;当导气孔直径小于其实际直径大小时,电机功率随着直径的减小而减小。
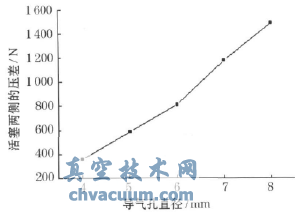
图5 活塞两侧压差随导气孔直径变化的曲线图
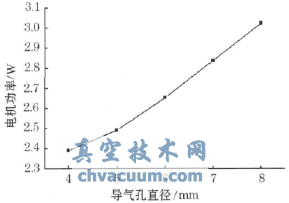
图6 电机功率随导气孔直径变化的曲线图
3、结语
减小节流管式调节阀的导气孔直径可有效降低电机功耗。通过对不同导气孔直径的调节阀内部流道进行三维稳态数值模拟以及节流管内部机械传动计算,得出流体对节流管端面处以及活塞两侧的压力,求出阀门在不同导气孔直径大小时的电机功率。分析得知:导气孔直径减小时,电机功率减小;导气孔直径增大时,电机功率也随之增大。