低压真空渗碳炉与传统渗碳炉的主要优势和特点比较
为了更全面掌握和了解,对有关低压真空渗碳炉与传统渗碳炉的主要优势和特点进行了比较,见下表。
真空渗碳与传统渗碳比较
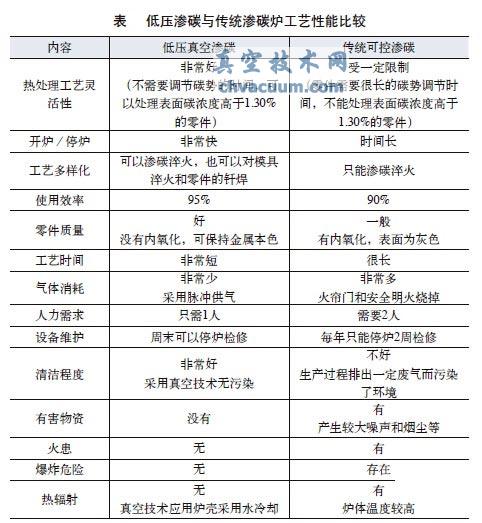
常规渗碳工艺温度受到炉子性能的影响,最高使用温度被限制在950℃以内,然而真空渗碳炉技术的改善可以将最高使用温度提高到1050℃。由于渗碳时碳的扩散系数随着温度的提高而加快,渗碳速度可以大幅度提升,使获得同样渗碳深度的时间大大缩短,有利于提高生产效率和降低生产成本。低压真空渗碳使用温度的提高为提高生产效率提供了先决条件。为此,在不影响零件力学性能的条件下,采用较高的渗碳温度可明显提高渗碳速度。常规和真空渗碳的典型工艺的比较见下表。
常规和真空渗碳的典型工艺的比较
采用AISI8620钢制造重载传动齿轮,进行同温度常规渗碳和真空渗碳达到同样有效硬化层深度试验比较见下表。
同温度常规渗碳和真空渗碳达到同样有效硬化层深度试验比较
可以看出,为了达到同样的渗碳硬化深度,不仅真空渗碳较常规渗碳节约74min(生产周期仅为常规82%),而且齿轮经过真空渗碳气淬硬化后表面仍可保持金属本色,没有内氧化发生,变形大幅度减小,为渗碳后期的磨削加工节省了难度和时间,质量水平和使用可靠性成倍提高(据了解,目前汽车行业的高端齿轮箱用齿轮,要求必须采用低压真空渗碳技术生产)。有人对大于要求渗碳深度1.60mm的重载货车齿轮进行渗碳时间对比,采用低压真空渗碳总渗碳时间仅为385min,而采用连续可控渗碳炉渗碳总时间需要12h,前者生产周期仅为后者的50%。这说明在提高渗碳质量的前提下,实际生产周期缩短是非常明显的。
大量试验数据证明,低压渗碳工艺技术获得的优良结果已经为广大用户所接受,尤其在常规渗碳难以解决的深层渗碳质量欠佳(长时间渗碳过程网状碳化物产生)的问题,采用真空渗碳实际渗碳时间的大大减少,其优越性表现的十分显著。
有人对真空渗碳与常规渗碳获得同样渗碳有效硬化层的情况进行对比,结果见下表。
真空渗碳与常规渗碳获得同样渗碳有效硬化层的情况进行对比
经大量渗碳齿轮对比发现,低压真空渗碳层的高硬化区一般均可达到常规渗碳的两倍以上,真空技术网(http://www.chvacuum.com/)认为这一特性具备使齿轮在渗碳并需要进行磨削加工后能够保持相当的有效硬化层提供保证。另外,低压真空渗碳避免了内氧化的产生,渗层质量更加优异,为齿轮可靠性和高寿命使用提供保证。