大口径液控蝶阀在闽江调水工程中的应用
福清市闽江调水工程峡南泵站水泵机组出口安装了大口径蓄能罐式液控缓闭蝶阀,以实现泵阀联动,开启和关闭,远距离自动控制,自动保压。该文针对该蝶阀使用过程中出现的一系列代表性故障进行原因分析,并提出故障处理方法。为改善液压油油质,提高蝶阀的运行稳定性和可靠性,油泵出油口处增设了双筒滤油器。实践表明,该措施效果良好。
1、概况
福清市闽江调水工程峡南泵站位于福建省闽侯县祥谦镇峡南村,管线全长54km。第一期泵站内装设一台立式离心水泵机组和二台卧式离心水泵机组,水泵出口设置蓄能罐式液控缓闭蝶阀,具体参数见表1。
表1 水泵机组参数
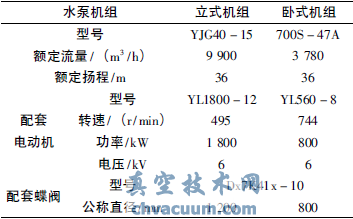
泵站自2000年2月21日正式投入运行以来,虽然也出现过导致泵组无法正常运行的故障,但液控蝶阀总体上能按预定程序实现泵阀联动,开启和关闭,远距离自动控制,自动保压。蝶体不抖动,流阻小,具有可调快、慢关两个阶段关阀,防止水锤危害,保护水泵及管网系统安全。
2、蓄能罐式液控缓闭蝶阀工作原理
蓄能罐式液控缓闭蝶阀(以下简称液控蝶阀)主要由蝶阀与液压工作站组成,安装于各类泵站的水泵出口,实现泵阀联动。该阀具有同时替代水泵出水管上的电动蝶(闸)阀、止回阀和水锤消除器的功能,液压系统工作原理如图1所示(图中虚线代表控制油路)。通过预设的启闭程序,液控蝶阀能自动实现水泵的缓开、速关/缓关,以防止断电水锤、泵组过速及反转对设备及管路造成的破坏。当液控蝶阀全开后,自动保压蓄能罐装置保证活门不产生摆动,使液控蝶阀在最小流阻状态下运行。
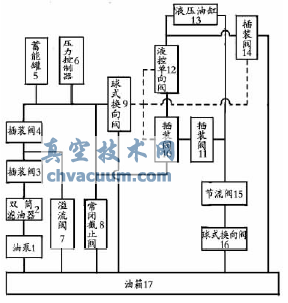
图1 液控蝶阀液压系统原理框图
液控蝶阀工作原理如下:
(1)开启。球式换向阀9和16上的电磁铁YV1和YV2同时得电,压力油使插装阀10和14关闭,液控单向阀12打开。油液经液控单向阀12、液压油缸13尾部的单向阀进入液压油缸无杆腔,推动活塞杆伸出,带动液控蝶阀活门向开启方向动作。有杆腔回油经节流阀15和球式换向阀16流回油箱。通过调节节流阀15,可得到要求的开阀时间。
(2)关闭。电磁铁YV1和YV2失电,压力油经插装阀10和11到液压油缸有杆腔,无杆腔回油经尾部快关调速阀、插装阀14流回油箱,实现快关。通过调节快关调速阀,可得到不同的快关时间。当阀门关至一定角度,液压油缸无杆腔回油经液压油缸尾部慢关调速阀、插装阀14流回油箱,实现慢关。调节慢关调速阀可得到不同的慢关时间。不同的切换角度可通过调节液压油缸尾部的慢关角度调节杆得到。
(3)任意位置停止(自保持)。开启或关闭过程中,如使电磁铁YV1得电,YV2失电,液控蝶阀的活门即停在任意位置。
3、液控蝶阀应用中典型故障分析处理
3.1、油压不能建立
2009年8月,大泵主阀操作系统转换开关处于单动位置。合上总电源开关和油泵电源开关,油泵开始向蓄能罐供油,直至压力达到额定工作压力17MPa为止,油泵停止工作。DN1200mm液控蝶阀单开按钮合上,打到全开位置时,油压瞬间下降至5MPa左右。而后油泵一直处于工作状态,油压也一直保持在10MPa附近,油压一直无法建立。
先分析认为,液压油含杂质,使插装阀10、11和14关闭不到位,液压油经过插装阀10、11、节流阀15和球式换向阀16流回油箱或经过液控单向阀12、插装阀14流回油箱,油泵打压出现无法升到额定值。拆开油箱,卸下电机、油泵,观察油箱内液压油油质情况。发现液压油变粘稠,含有一些颗粒物等杂质。对液压油采用过滤处理。拆卸插装阀10、11、14,球式换向阀9、16,用柴油清洗干净后重新安装。重复上述工作,油压一直保持在10MPa附近,油压还是无法建立。故排除了油质问题。
接着考虑是否液压油缸及油管路各密封件出现损坏而导致液压油泄漏严重。该蝶阀设两个蓄能罐。先关闭蓄能罐5-2的截止阀,打开蓄能罐5-1的截止阀,合上总电源开关和油泵电源开关,油泵开始向蓄能罐5-1供油。打压直至压力达到17MPa后,关闭蓄能罐5-1的截止阀,拆掉液压油缸尾部的高压胶管,关闭电源,使球式换向阀9和16上的电磁铁YV1和YV2处于失电状态。打开蓄能罐5-1的截止阀,蓄能罐内的压力油开始经插装阀10、11流到液压油缸有杆腔。结果发现,液压油缸尾部(无杆腔处)有液压油不断流出。拆卸液压油缸推杆、活塞发现,两个Y型圈密封件磨损变形。更换两个Y型圈密封件,重新安装液压油缸等部件。经真空技术网(http://www.chvacuum.com/)调试运行,上述故障现象排除,油泵可以正常建压。
3.2、电机空转
2010年6月,小泵主阀操作系统合上总电源开关和油泵电源开关,油泵压力始终停在0(原始位置),油泵电机一直顺时针方向旋转。停机拆卸电机、油泵,发现电机、油泵连接处的圆形轴套断裂缺角,导致固定键脱落,电机处于空转状态。更换圆形轴套或焊接断裂缺角部分后,上述故障现象消失,小泵液控蝶阀可以正常工作。
3.3、卧式离心水泵缓慢反转
2010年11月,卧式离心水泵停机,DN800mm液控蝶阀活门关到位后,卧式离心水泵出现缓慢反转现象,出水口钢管段有水回流声音。分析认为,该现象可能是液控蝶阀活门密封面泄漏所致。液控蝶阀长时间运行使用,造成密封圈磨损或密封面接触过盈量太小。通过拧紧布置在液控蝶阀活门周边上的压紧螺钉,调整活门密封圈,补偿磨损量。经此处理后,水泵没有出现反转,液控蝶阀正常工作。如果液控蝶阀活门橡胶密封圈磨损严重,则需要及时更换。
3.4、液控蝶阀无法打开
2011年3月,在润滑油质及控制系统正常情况下,DN800mm液控蝶阀无法打开。经分析判断,蓄能罐5-1不能保压,氮气压力不够,需充气。关闭蓄能罐5-1的截止阀,打开蓄能罐5-2的截止阀,让蓄能罐5-2处于工作状态,液控蝶阀活门可以正常打开,证实了蓄能罐5-1不能保压。随后对出现问题的蓄能罐进行了漏气及皮囊破损检查,并进行相应的处理。
3.5、液压操作系统油泵启动频繁
2011年12月,大泵主阀液压操作系统油泵启动频繁。转换开关处于联动位置,合上总电源开关和油泵电源开关。当水泵在运行状态时,DN1200mm液控蝶阀油泵短时间运行后,油压能够达到额定值17MPa,但维持时间很短,大约15min,很快下降到油泵启动值14.5MPa,致使油泵频繁启动,以维持正常油压,给设备安全运行带来隐患。
现场对液控蝶阀系统及外观进行全面检查。润滑油质为新更换的抗磨液压油,油质情况正常。液控蝶阀外部无明显的漏油点,溢流阀工作正常,液压油缸活塞处两个Y型圈密封件已更换,基本上可以排除油压系统漏油的可能性。经过分析判断,球式换向阀9和16阀芯可能存在内漏,密封不严,致使压力油短路,造成油压下降过快。对球式换向阀9和16进行解体检查发现,前者阀芯有明显裂纹。更换该球式换向阀后,经调试运行,上述故障现象排除,油压稳定,油泵打压可以正常工作。
4、液控蝶阀应用经验总结
从液控蝶阀十多年运行中出现的故障现象看,故障原因一般可考虑以下几个方面,并逐个排查。
(1)不能开阀:①检查油泵转向是否对,正常应顺时针方向旋转。②常闭截止阀未关闭。③流量控制阀被关死。可打开并慢慢上调。④溢流阀压力调得太低或失效。需检修。⑤电磁阀阀芯卡阻。需拆下检修。⑥其它阀门外泄漏严重。需拆下调整或检修。
(2)开泵时间过长或不能停机:①检查滤油网是否堵塞,吸油管是否漏气。②流量控制阀是否调得太小。若是,可适当调大。③溢流阀压力调得太低或失效泄漏。需检修。④油泵出油管是否泄漏。⑤全开行程开关未到位,自动保压未启动。⑥常闭截止阀关闭未到位。
(3)泄漏严重,保压效果不佳:①电磁阀孔内杂物造成泄漏。检查滤网是否良好,可开机多次冲去杂物。②常闭截止阀未关紧。③主油路中插装阀有杂物。需清洗检修。④蓄能罐充气压力不够。需充气。⑤油管路密封件损坏。需更换。
离心式水泵启动前,运行人员往往忽视液控蝶阀油泵打压是否正常,误认为只要油泵打压能升至17MPa即可,对油压具体情况没有进行仔细检查,容易造成液控蝶阀运行中产生故障。故液控蝶阀液压系统在运行前要认真检查。
实际运行中,需定期检查液压油油质情况。不符合清洁度和润滑性要求的,要更换液压油,同时更换滤油器滤芯,彻底清洗油箱。应定期检查油箱油位。液压装置投入运行后,需经常到现场观察运行情况,查看是否有故障指示、漏油等异常现象发生。如有,需及时处理。
5、液压系统改进措施
油质情况直接关系液控蝶阀能否正常开启或关闭。液控蝶阀运行中,原先使用46号防锈汽轮机油,使用一段时间后,油质变差,并含有一些颗粒物等杂质。后来改用YB-N32抗磨液压油,油质情况得到改善。原液压系统在球式换向阀16至油箱的回油管路上设置滤油器,液压油过滤效果不佳。后采用在液控蝶阀柱塞油泵出油口处增设双筒滤油器,即在油箱外壳上面卸掉油路连接管,增加一些管路连接件与双筒滤油器对接,后者焊在出口钢管管壁上,以便操作。该双筒滤油器由二组过滤筒组成,互为工作与备用,可实现不停机切换过滤筒,不停机清洗或更换滤芯,保证主机正常连续工作。液控蝶阀柱塞油泵出油口处经增设双筒滤油器后,因液压油质问题出现异常而导致的故障现象基本没有发生。
6、结语
福清市闽江调水工程峡南泵站水泵机组出口安装了蓄能罐式液控缓闭蝶阀,十多年的运行过程中,虽然也出现了一些故障,但总体状况不错,达到了预期的目的。实践表明,要保证蓄能罐式液控缓闭蝶阀正常工作,最关键的是要加强维护,及早发现问题,及时处理;坚持每个大修期更换全部密封件,每个小修期换油滤油,检查调试,清洗油箱。油泵出油口处增设双筒滤油器,可改善液压油油质,提高水泵出口液控蝶阀的运行稳定性和可靠性。