高压大口径全焊接阀体管线球阀国产化历程
一、历程
2000年之前,我国拥有2万km长输管线,只占全世界260万km管线的0.8%。全焊接阀体管线球阀无一例外地采用美国Cameron公司产品。 2000年之后,在国家关于开发西部,使用绿色能源的政策指导下,起动西气东输一线工程,从新疆轮南至上海,全长4200km,管径42″(1″=25.4mm,下同),输送压力10MPa。其中全焊接阀体紧急切断阀全部采购国外产品,分体式锻钢阀体管线球阀则由上海耐莱斯·詹姆斯伯雷阀门有限公司供货。与此同时,国家发改委提出《全焊接阀体管线球阀》国产化计划。四川自贡高压阀门股份有限公司取得国家财政支助,从意大利新比隆(NewoPignone)公司引进全套全焊接阀体管线球阀技术资料、工艺和装备,2003年试制成功第一台全焊接阀体管线球阀。上海耐莱斯·詹姆斯伯雷阀门有限公司在国家财政支助下,联合高校,发挥地区优势,自主开发研制全焊接阀体管线球阀,于2005年试制成功筒状和球状的阀体全焊接管线球阀,并拥有自主的知识产权,可以提供Class600,DN800(NPS32)以下管线球阀,且在涩宁兰复线上服役。
2008年西气东输二线工程的起动,从新疆到上海再到广州,全长8800km,选用管线直径DN1200(NPS48),输送压力12MPa,这样就需要Class900,DN1200(NPS48)全焊接阀体管线球阀。这种高压大口径全焊接管线球阀,2007年在全世界服役的仅13台。二线工程的主干线上,40″Class600以上的紧急切断阀亦全部从国外进口。32″以下在国内采购。同时,在国家能源局的主持下,2009年4月在沈阳召开“天然气长输管线关键设备国产化”工作会议,张国宝主任和中石油廖永远副总经理参加会议,指示大口径高压全焊接管线球阀国产化,应予立项,这对降低西气东输工程造价,保证国家能源供应的安全,振兴装备制造业具有重要意义。并于2009年11月23日在北京钓鱼台国宾馆召开天然气长输管道关键设备国产化启动及签约仪式。中石油与上海耐莱斯·詹姆斯伯雷阀门有限公司签订10台Class600,Class900磅级,口径DN1000,DN1200大口径高压全焊接阀体管线球阀的技术开发合同。在6个月的生产周期内完成了试制任务,并于2011年通过工业性运行试验,产品已在西气东输三线服役。
十年磨一剑,我国已完成高压大口径全焊接阀体管线球阀的国产化工作,可以为国内外提供压力等级从Class150,25001b级(11b=0.45kg),通径从2″~60″球状或筒状全焊接阀体或分体式阀体的管线球阀。图1为上海耐莱斯·詹姆斯伯雷阀门有限公司生产的Class900,48″高压大口径全焊接阀体管线球阀。并与2012年4月承接西气东输三线Class900,48″全焊接阀体管线球阀32台,2012年年底完工正式交付使用。
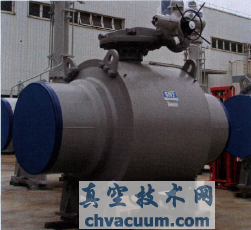
图1 Class 900.48''高压大口径全焊接阀体管线球阀
二、创新
和管道工业一样,2000年我国全焊接阀体管线球阀落后于国外近半个世纪。然而,我国开发这一全焊接产品是在21世纪,可以充分运用现代化设计技术与现代制造技术,起步晚但起点高。整个开发过程一方面应用反求工程,消化吸收国外各个阀门公司之所长,综合为我所用;另一方面运用现代数值分析方法来解决产品设计和焊接工艺上的技术问题,运用现代断裂学理论解决大厚度窄间隙埋弧焊焊缝免焊后热处理的技术难点。因此,在研制开发过程中,有很多方面拥有自行的知识产权,取得国际领先地位。
1.阀体强度的应力分析
早于2004年,采用ASMEⅧ锅炉压力容器第二分册分析法,通过有限元分析,计算在外载荷与内压复合作用下阀体的应力强度。提出筒式阀体在阀颈处存在应力集中,建议采用焊接阀颈结构。这一分析和建议已被国内外主要阀门公司认可和采用。
2.低残余应力焊接工艺参数的优化
全焊接阀体管线球阀的关键技术是焊接,其难点是焊接最后一道工序不能进行热处理。因此,对焊接过程的温度场、应力场和焊接变形进行预测和控制,上海耐莱斯·詹姆斯伯雷阀门有限公司与上海交通大学合作,首先用数值分析方法对焊接过程温度场,应力场进行预测和控制,采用“固有应变法”对阀体焊接变形进行预测和控制(见图2),并与实际测定的温度场,残余应力和变形值相比较,从而优化焊接工艺参数在较低的残余应力水平上,为焊后免热处理提供条件。
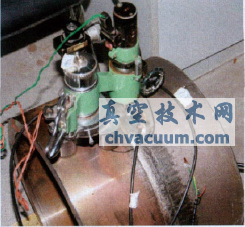
图2 应力场的测定
3.焊缝免焊后热处理(PWHT)的安全评估
根据API6D与ASME标准的相关规定,大于38mm以上厚度的焊缝必须进行热处理,而产品中有橡胶弹性体,不能进行热处理,国外的阀门公司无一对此做出科学的解析和安全评估。国内首先应用断裂学理论,按照英国BS7448第二部分《断裂韧性试验》的方法,采用美国API1104附录A《管道焊接与相关设施》的评定与验收标准,对全焊接阀体焊缝试样做全厚度断裂性CTOD试验以及残余应力测定,根据结果做出免焊后热处理的安全评估。图3为在液压万能试验机上,CTOD试验过程,试验温度-46℃,二次加载直至试验失稳。
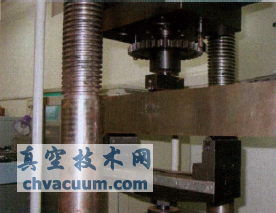
图3 CTOD试验预制疲劳裂纹试验过程
4.过渡段材料的优化
运用筛选工程,对国外阀门公司采用A694《高压传送设施法兰管件、阀门材料和零件用锻造碳钢和合金钢材料》标准中的F60、F52作为过渡段材料提出质疑。这一标准既不是阀门标准B16.34的引用标准,又不是管道标准B31.8的引用标准,没有标准支持,是选用错误。这一结论已被美国工程师协会ASMEB16.34专业委员会和美国试验和材料协会ASTMA694专业委员会的答复中被确认,从而使我国长输管线工程的安全性得到进一步保证。
三、崛起
高压大口径全焊接管线球阀的国产化过程,亦是传统制造业改造成现代先进阀门制造业的过程,现代先进制造业是一个技术经济群体,是指将原材料和其他生产要素,经济地、合理地转化为高附加值、高技术产品的一个基地。拥有现代设计技术,现代先进制造装备和制造工艺以及系统化的现代化管理技术。在高压大口径全焊接阀体管线球阀的国产化过程中,上海耐莱斯·詹姆斯伯雷阀门有限公司充分运用现代设计技术,如应用反求工程技术,解决阀体材料的化学成分和机械性能;运用筛选工程技术提出用A350LF6材料替代国外传统的A694F60材料作为阀体过渡段用材;运用数值分析方法,指出传统阀体设计中应力集中,采用焊接阀颈优化阀体结构设计;运用数值分析方法,精确地预测阀体的焊接变形,优化焊接残余应力的焊接工艺参数;运用弹塑性断裂力原理论解决焊缝免焊后热处理的安全评估和验收标准;运用数值分析法对阀体在外载荷和内压复合作用下的应力强调分析和抗震计算。
在装备上,拥有从意大利进口的车磨一体化的大型球体数控车球磨磨球机(见图4),拥有大型数控立车和大型卧式镗铣加工中心,以及全国首台3200t液压试验设备、自动埋弧焊机(见图5)、美国进口三坐标测试仪,大扭矩测试传感器及火烧试验等现代化先进的阀门制造装备和试验设备。
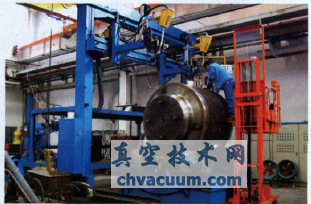
图4 大型球体数控车球磨磨球机
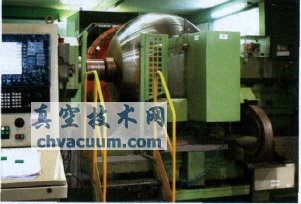
图5 自动埋弧焊机
上海耐莱斯·詹姆斯伯雷阀门有限公司在国家发改委和能源局的直接领导下,取得高压大口径全焊接阀体管线球阀批量生产成功,并在通过工业性试验的基础上,上海电气集团将投资扩建7000m2大口径管线球阀的装配、焊接、试验生产线,添置超大型4500t液压试验设备和3.15m大型数控立车,形成年产40″~60″管线球阀150台,36″以下管线球阀1500台的能力,建成一个现代化先进的阀门制造企业,为我国管道工业作出贡献。