L型进渣阀进渣特性试验研究
在L型进渣阀半工业试验台上,针对表观引渣风风速在0~25m/s、引渣风管深入比例0~0.6、联箱压力0.05~0.15MPa、试验物料粒径1.32 ~2.22mm时,对该进渣阀的进渣特性进行了试验研究。试验结果表明:随着表观引渣风风速增大,进渣阀进渣速率先增大后减小;进渣速率随引渣风管深入比例的增大、试验床料颗粒平均粒径的增大而减小,随联箱压力的增大而增加。此外,还得到了进渣特性的关联式,关联式的计算值与测量值吻合较好,可用于指导进渣阀的调节。
引言
循环流化床锅炉的稳定运行需要合适且稳定的炉膛床压以及正常的流化,而炉膛床压的控制是通过炉膛底部排放底渣来实现的,同时从炉膛底部排出粗颗粒及焦块以防止进一步的结焦。当锅炉燃用煤种为低热值煤种时,其灰分通常占到40%-60% ,甚至更高。由于CFB锅炉底渣含有大量的物理热,因此当灰渣不经过冷却直接排出时,灰渣物理热损失可超过3%。如果灰渣物理热采用汽机冷凝水冷却回收,又会因排挤抽汽而带来较大的汽机侧冷源热损失。因此在CFB锅炉燃烧劣质煤时,应尽量采用流化床冷渣器,通过空气和高压给水吸热,将底渣物理热回收到锅炉中。为此,课题组开发了混流式流化床冷渣技术,并已投入工业应用。该冷渣器配有一种在结构上可调节的L型进渣阀,该进渣阀是在常规L阀的基础上加装可伸缩的喷气管而形成的,其基本工作原理与L阀相同,但工作特性有所不同,主要不同点在于:该L阀处理的不是细颗粒,而是较粗的锅炉底渣。
国内外学者对对L阀的研究较多,但主要集中在粒径小于90μm的Geldart-A类颗粒和90~650μm的Geldart-B类颗粒,而对于颗粒尺寸及密度较大的Geldart-D类颗粒的研究则很少。但实际循环流化床锅炉排出的底渣则是具有宽筛分特性的颗粒,D类颗粒所占比例可达50%乃至更高。
为进一步掌握该进渣阀在处理底渣床料时的气固流动特性,本研究对混流式流化床冷渣器配套的进渣阀的气固流动特性进行了较系统的试验研究,其研究结果也可用于其它类似系统的进渣控制。
1、试验系统
1.1、试验系统
试验系统由3部分组成: 试验台本体、送风系统和试验数据采集系统。
试验台本体包括立管、排渣导管、引渣风管、冷渣器本体、排渣称重盒。立管直径219mm,高600mm;排渣导管直径159mm,长400mm。数据采集系统包括采集压力分布的KYB14A型差压变送器、Adam4117型号压力模块、Adam4520 型号转换模块及工业计算机。试验系统如图1所示。
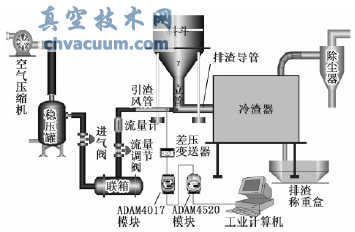
图1 冷态试验装置系统
1.2、试验物料及方法
试验物料采用引进技术制造的某300MWCFB锅炉底渣,粒径范围0~20mm,堆积密度1430kg/m3,真实密度2419kg/m3,平均粒径1.32mm。试验物料粒径分布如图2所示。
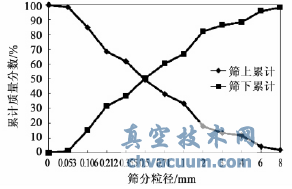
图2 试验物料筛分特性曲线
试验过程中,分别调节引渣风管喷嘴出口处的表观引渣风风速、引渣风管在阀体内的深入比例(即引渣风管深入阀体立管段的长度与立管直径的比值,如图1中深入比例XL=0.5) 、引渣风来流处联箱压力和试验物料平均粒径。试验时间30~60s。数据采集系统记录各试验工况的时间和压力,进渣量由排渣称重盒称取,并反复进行多次试验,在进行方差检验后对实验结果取平均值以便计算进渣速率。
2、进渣特性的试验结果及分析
2.1、表观引渣风风速对进渣特性的影响
图3为引渣风管深入比例分别为0、0. 2、0.4时的表观引渣风风速对进渣特性的影响。引渣风管深入比例为零时,当表观风速达到7.37m/s时系统开始进渣。随表观风速增加,进渣速率增大。当表观风速为15.98m/s时,进渣速率达到最大值8.46kg/s。随着表观风速的进一步增大,进渣速率开始逐渐减少,最终稳定在7.15kg/s。即存在一个转折风速,表观风速小于该转折风速时,进渣速率随表观风速的增加而增加; 表观风速大于该转折风速时,进渣速率随表观风速的增加而减小。引渣风管深入比例为0.2~0.4时也同样存在转折风速,其值分别为11.05和9.21m/s。存在转折风速的原因在于:进渣阀在运行时,进渣所需要的压头由立管段的料位提供,该压头存在一个最大值,其值为该料位下的床料处于临界流化时对应的床层压降。在本试验中,料斗的截面尺寸为1.2×0.8m,立管段的直径为0.219m,在试验过程中料斗料位高度变化不超过0.2m。根据张伟等人的研究,此时料位波动对进渣速率的影响很小;而随着表观风速的增大水平管段的阻力是逐渐增加的,这就导致了该进渣速率在随表观风速增加的过程中存在一个最大值。另外,随着深入比例的增加,所需的启动表观风速及最大进渣速率值均减小。
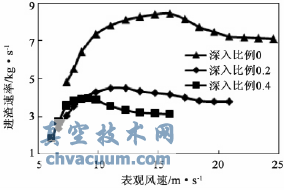
图3 进渣速率与观引渣风风速的关系曲线
2.2、引渣风管深入比例对进渣特性的影响
表观引渣风风速分别为7.37、8.6、9.82和11.05m/s时引渣风管深入比例对进渣特性的影响如图4所示。由图可见,随着引渣风管深入比例的增加,引渣风管喷嘴前端可被吹动的物料量减少,阀体内因不易流动所引起的死区所占比例增大,因此进渣速率大体上呈现出减小的趋势。但在表观引渣风风速较小为7.37m/s时,进渣速率先减小后增加而后又减少。这是由于在引渣风管深入比例的增加的同时,试验物料在水平管段中运动所受到的阻力也在相应地减小。
2.3、联箱压力对进渣特性的影响
图5为联箱压力分别为0.05、0.1和0.15MPa时进渣特性曲线图。随着联箱压力的增大,进渣速率呈现出不同程度的增加。主要原因是:当联箱压力变大而流量保持不变时,由于管路的沿程阻力损失是一定的,因此引渣风的压头变大,引渣风气流的动量增大、刚性增强,其携带能力增强,导致进渣速率增加2~15%不等。在表观引渣风风速越大时,联箱压力对进渣特性的影响更为显著。
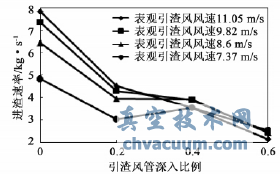
图4 进渣速率与引渣风管深入比例的关系曲线
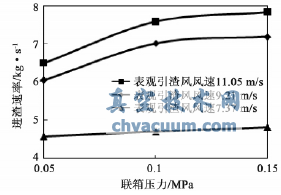
图5 进渣速率与联箱压力的关系曲线
2.4、颗粒物性对进渣特性的影响
图6为颗粒粒径分别为1.32、1.92和2.22mm时的进渣特性曲线。表观引渣风风速相同时,随着试验床料中4mm以上粗颗粒含量的增加,试验物料的平均粒径由1.32mm增大至2.22mm,气流与固体颗粒之间的物性差异增大,气流在延伸和前进过程中的动量消耗增加,气流动量及刚度减小,因此在相同表观引渣风风速下所能获得的进渣速率减小。另外由于不同颗粒平均粒径下的最大进渣速率由8.46降至5.62kg/s,对应转折风速也相应地由15.96减少到12.28m/s。
2.5、进渣特性的关联式
试验表明,影响进渣阀进渣特性的因素有:表观引渣风风速υ、引渣风管深入比例XL、引渣风来流联箱压力p、颗粒平均粒径dp、转折风速vmf。通过无量纲分析,可确定进渣特性关联式为:

式中:GP—进渣速率,ρg—气体密度,D—进渣阀立管段直径,υ—气体运动粘度,ν—表观引渣风风速,νmf—转折风速,p—引渣风来流联箱压力,p0—大气压,XL—引渣风管深入比例,dp—颗粒平均粒径,A、a、b、c、d均为常数。
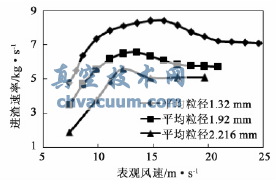
图6 不同颗粒平均粒径下的进渣特性曲线
通过对转折速度进行拟合,发现该转折速度与引渣风管深入比例及颗粒平均粒径有关,因此拟合得到转折风速的关联式为:

将实验数据代入式(1)进行回归,得到进渣特性关联式为:
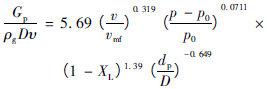
公式(3)的适用范围:
表观引渣风风速ν:6.14~24.56m/s
颗粒平均粒径dp:1.32~2.216mm
联箱压力p:0.05~0.15MPa
渣温:室温
图7为进渣速率GP的计算值与测量值的比较。结果表明,式(3)的拟合相关度较好,误差在25%以内。
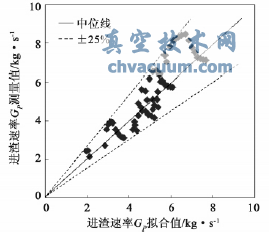
图7 Gp拟合值与测量值的比较
3、结论
(1)试验表明随着表观引渣风风速的增大,进渣阀的进渣速率呈现出先增大后减小的趋势,即存在一个转折速度,在该速度下可获得更经济的进渣速率。实际运行中表观引渣风风速的选取可以将转折速度作为参考依据;
(2)随着引渣风管深入比例的增大、颗粒平均粒径的增大,进渣速率减小; 随着联箱压力的增大,进渣速率逐渐增加,且表观引渣风风速越大时更为显著;
(3)对试验数据进行多元回归分析,分析得到了进渣阀进渣特性的关联式。关联式计算值与测量值吻合较好,可用于相应参数条件下进渣速率的计算,为进渣特性提供了理论依据。
由于电厂现场的压缩空气压力通常在0.5~0.7MPa左右,而且底渣的温度高达850℃甚至更高,因此在更高压力引渣风条件及高温条件下的进渣阀的气固流动特性,还需要进一步的试验研究。