废热锅炉底部调节阀复杂控制的应用
废热锅炉底部的调节阀既要控制废热锅炉底部的液位,也要对废热锅炉反冲洗进行控制,因此对调节阀的控制成为工艺上的难点。为此,设计一套控制方案,实现了此调节阀两种控制的自动无扰切换和协调,将其应用于某煤制天然气项目的气化炉,获得了较好的控制效果。
气化炉是煤制天然气工艺中的关键设备,目前应用较多的是碎煤加压气化炉,其优势有:自热式工艺,所需热量由煤的部分燃烧提供;加压有利于气化炉中反应效率的提高。废热锅炉是气化炉不可缺少的部分,气化炉产生的粗煤气中含有大量的煤、灰及焦油等杂质,在离开气化炉后进入洗涤冷却器,然后进入废热锅炉进行废热利用和进一步的洗涤,洗涤所用到的介质为煤气水,并且在废热锅炉底部和洗涤冷却器之间通过循环泵进行循环,以实现洗涤后含有煤尘和冷凝焦油的煤气水都能通过废热锅炉底部管线排出。因此,洗涤所用的高压煤气水需不断地补入,以保持废热锅炉底部的液位。洗涤后的粗煤气从顶部离开废热锅炉后,再由气液分离器进行分离后,进入下一界区,气液分离器产生的煤气水再返回废热锅炉进行循环利用。
1、工艺介绍
图1所示为某煤制天然气项目气化炉的废热锅炉工艺流程图。气化炉在正常运行时,废热锅炉底部的液位要控制在合理范围内,液位过高时,增加了粗煤气进入废热锅炉的阻力,且会导致粗煤气中含有大量的水蒸气;液位过低时,由于进入废热锅炉粗煤气温度为181℃左右,而废热锅炉的正常操作温度在161~175℃之间,液位过低将会使废热锅炉运行于较高温度下,对设备造成损坏。因此,在废热锅炉下部设计了调节阀,以实现液位的自动控制。
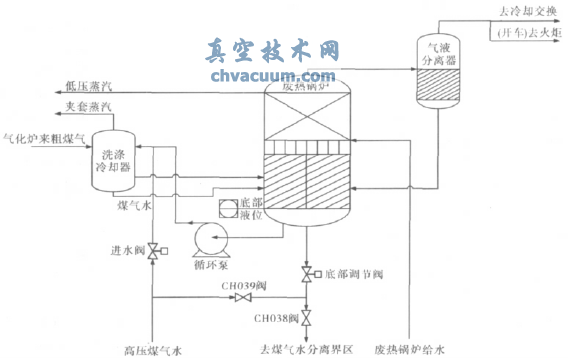
图1 气化炉废热锅炉工艺流程
气化炉运行过程中,粗煤气带出的煤粉、灰与焦油在废热锅炉中积聚,会造成废热锅炉底部堵塞,造成废锅底部液位的升高,当超过粗煤气进气孔时,会导致进气阻力明显增大,导致洗涤冷却器出口温度升高,进而影响粗煤气和煤气水的正常运转,为防止上述情况的发生,需设置自动反冲洗装置,对废热锅炉进行定期的反冲洗,反冲洗作用将废热锅炉中沉积的杂质与煤气水充分混合,通过底部管线排出废热锅炉。工艺过程控制上的难点包括:
a.反冲洗顺序控制与液位自动控制两种策略作用时间的分配,相互切换时的自动、无扰动设计。根据上述的工艺要求,反冲洗顺序控制为周期循环控制,防止阀门与管线堵塞,但气化炉处于正常工况下,要始终投入废热锅炉液位的自动控制。
b.反冲洗顺序控制,是一个自动的、无需人工操作的过程,必须严格按照工艺要求、反冲洗步骤进行设计,且要考虑到顺序控制过程中出现的各种意外情况。
c.当执行反冲洗顺序控制时,废热锅炉中只有进水,无排水,所以液位会有明显变化,则要求调节阀的液位自动控制必须有较高的调节品质。
2、解决方案
针对上述的某煤制天然气项目废热锅炉底部液位自动控制由PID控制实现,液位由现场的双法兰差压液位计检测,再根据调节阀的特性,设定合理的PID参数,以获得最佳的调节品。反冲洗顺序控制由程序实现,具体程序流程如图2所示。
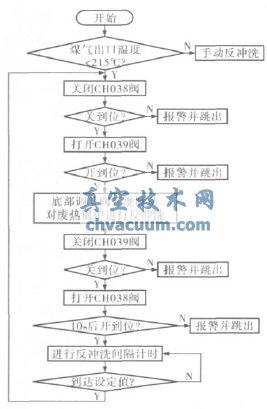
图2 反冲洗顺序控制程序流程
废热锅炉正常运行工况时,CH038阀门、底部调节阀均打开,将含杂质的煤气水排出废热锅炉。当粗煤气出洗涤冷却器温度超过某定值时,反冲洗程控不允许投入,但可以手动反冲洗,若是因废热锅炉堵塞导致,需到现场进行疏通处理。只有粗煤气出洗涤冷却器的温度低于某定值时,反冲洗程控才允许投入。具体操作为:先点击“A”,再点击“S”,程序控制开始,自动关闭CH038阀门,打开CH039阀门,使高压煤气水反冲废热锅炉底部,操作人员可根据工况变化,手动设定底部调节阀的开度脉动的峰值、谷值、长度和周期,使高压煤气水具有一定的冲击力,将沉积下的杂质与煤气水混合,以达到反冲洗的目的。本次反冲洗结束后,关闭CH039阀门,打开CH038阀门,底部调节阀恢复到程序控制投入前的状态。程序控制进行反冲洗间隔计时,到达间隔计时的设定值后,反冲洗程序控制再自动投入。若程序控制执行时,阀门出现未开、关到位的情况,程序控制会自动退出,保证设备处于安全状态,且发出报警信息。反冲洗画面下部为底部调节阀开度的实时趋势,便于操作员观察程序控制的状态。另外,操作员根据实际工况,在任何时间都可以通过点击“M”,就可将程序控制切除。
两种控制策略均对底部调节阀作用,废热锅炉的反冲洗程序控制为循环运行,除了反冲洗运行的时间以外,其他时间均为液位的自动控制,针对两种控制运行时间的分配、切换,笔者所设计的解决方案如图3所示。
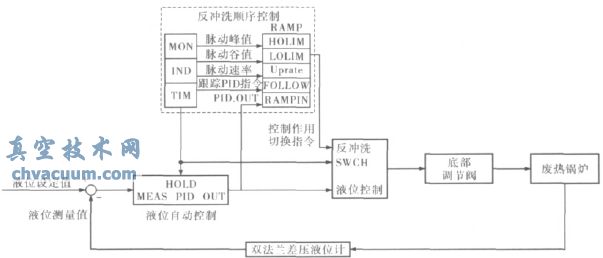
图3 底部调节阀控制方案
当液位自动控制切换到反冲洗程序控制时,控制程序发出指令,使程序控制开始作用,调节阀接收程控的指令而进行开度的变化,此时液位PID控制仍为自动状态,但不对阀门作用,且PID的输出保持在切换时的数值;当反冲洗程序控制切换到液位自动控制时,控制程序发出另一指令,阀门开度立即回到PID所保持的开度数值,液位PID控制立即恢复作用,调节阀门对液位进行控制,此时反冲洗程控不对阀门进行控制,进入反冲洗间隔计时,等待下一次程控的执行,但在间隔计时过程中,反冲洗程控时刻跟踪液位PID控制的输出。
通过上述的方案设计来实现两种控制策略的时间分配、无扰动切换。由于反冲洗程控作用时,高压喷射煤气水只进入废热锅炉,但无出口排出,因此程控结束后,液位会有较大的升高,所以液位自动控制应根据调节阀的特性,设置最优的PID控制参数,实现液位控制的快速性、稳定性和准确性。
3、应用效果
将笔者设计的控制方案投入到实际的工程中,需对该控制方案分步投入、调试,实现液位PID控制参数的最优化、程序控制的完善化,最终得以在实际工程中有效应用。
3.1、液位自动控制
为实现底部调节阀对液位的自动控制,需对PID控制器的参数进行调试、优化,以获得最佳的调节品质。
当P=2、I=60s时,液位设定值由55%下降至50%,控制的超调量为2.78%,稳定时间为300s,液位自动控制的效果如图4a所示;当时,液位设定值由55%下降至50%,控制的超调量为3%,稳定时间为147s,液位自动控制的效果如图4b所示。
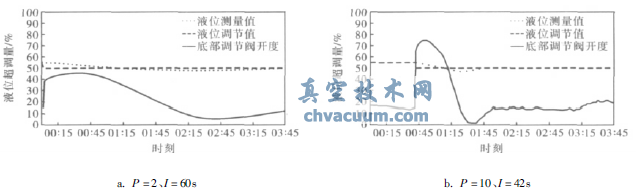
图4 液位控制效果
通过上述两种在不同参数下的控制效果图的对比可知:参数为第二种情况时,液位控制的超调量变化不大,且实现了的液位的快速稳定,控制品质最佳。
3.2、反冲洗程序控制
反冲洗程序控制单独投入使用时,程序控制画面中所有参数均由操作人员根据实际工况进行设定。反冲洗程控涉及3个阀门的状态:CH038阀、CH039阀均按程序进行开、关动作;底部调节阀按所设定的参数进行脉动。反冲洗程序控制完全实现了工艺上对反冲洗控制的要求。
3.3、液位自动控制与反冲洗程序控制联合作用
经过液位PID控制与反冲洗程控的单独调试后,再将二者结合起来,共同投入到现场设备的控制中,根据实际的控制效果,继续进行优化、提高调节品质。当反冲洗程序控制退出后,液位PID控制立即恢复作用,此时液位已分别上升4.41%和8.54%,但通过PID控制,分别经过49、200s,便将液位调节稳定。因此可以得出:无论废热锅炉运行于何种工况下,笔者设计的控制方案都能顺利完成反冲洗控制,且能快速调节稳定液位,获得了较好的控制效果。
4、结束语
根据控制方案实际应用的效果图,可以看出笔者所设计的控制方案:液位PID控制与反冲洗程序控制自动、无扰切换,大大减小了操作人员的工作量;液位PID控制具有较高的调节品质,反冲洗程序控制操作简单,参数修改方便,完全按照工艺要求进行控制。笔者设计的控制方案,不仅解决了运行控制上的难点,而且实现了工艺的要求,获得了满意的效果。