液动执行机构在催化裂化装置的应用
电液执行机构具有控制准确、稳定性好、可靠性较高的特点,在催化装置中应用越来越广,本文从工作原理、运行中出现的问题及处理进行了论述并提出了相应改进方案,并对电液执行机构的发展进行简单说明。
随着催化裂化装置运行周期不断延长,关键设备运行稳定性、可靠性能对运行周期直到决定性作用,电液执行机构就是催化装置中关键调节控制设备之一,它在装置滑阀、蝶阀、机组静叶调节系统和汽轮机调速系统上大量应用。如在反、再系统单动滑阀控制催化剂的循环量,保证反、再系统的能量平衡;再生器出口的双动滑阀或蝶阀控制再生器压力,保证反、再系统的压力平衡;在轴流风机系统采用电液执行机构对静叶角度进行调节,控制主风系统流量;在汽轮机组调速器系统电液执行机构也逐步开始应用,调节汽轮机组转数以控制反应系统压力。在正常生产条件下,要求电液执行机构工作状态稳定、控制平稳、可靠性高,在故障状态下动作准确,尤其是在自保投用情况下动作一定准确、使控制主体迅速达到自保位置,保证装置安全、保护机组。本文依据电液执行机构在运行中的问题及处理进行了探讨,提出了具体的改进方案,并对其发展方向进行了简述。
1、电液执行机构的工作原理
电液执行机构是由电气控制系统、电液伺服油缸、油泵及位移传感器等组成。当电气控制系统输入端接受4-20mA输入主令信号经规格化处理转换为0-10V电压信号,同时接受位移传感器现场测得的实际阀位,经过规格化处理转换为0—10V电压信号,二者在伺服放大器中比较产生差值信号,经电压放大、功率放大后驱动电液伺服阀,控制油缸的运动方向,从而带动执行机构按照规定位置动作,直至输入信号与位移传感器反馈信号偏差值为零,这时伺服阀的控制电流也接近零,伺服阀蕊处于中位,无液压油输出,使油缸中活塞停留在与输入信号相对应的位置上,从而达到电液执行机构自动控制的目的。
2、滑阀、蝶阀电液执行机构运行中故障处理及改进措施
2.1、液压控制元件运行中的问题
2.1.1、电液伺服阀
伺服阀作为液压控制元件是非常关键的元件,它的性能决定控制精度和动态的稳定性,它的可靠性决定了整个控制系统的使用寿命。它的作用是将较小的电功率信号转换成较大的液压功率输出,实现信号的电/液转换,即完成放大作用。
早期电液伺服阀采用的是双喷嘴挡板式结构,其对液压油清洁度要求较高,必须保证清洁度NASI638A不低于7级,在运行过程中易出现阀堵塞现象,造成执行机构误动作,严重的出现阀位跑“单向”,造成工艺生产较大波动。现阶段射流管结构伺服阀应用较多,其结构上采用干式力矩马达,整体焊接,射流管为先导极,滑阀阀蕊作功放,是一种高性能力反馈两组方向流量控制阀,具有抗污染能力强、可靠性高、分辨率高的特点,尤其是在射流管堵塞状态下,伺服阀一般保持原阀位,基本上避免了跑“单向”现象的出现,安全性有了很大的提高。
在实际运行过程中液压油使用也是影响伺服阀运行状态的因素之一,在北方地区或冬季使用N32低凝液压油,热带地区或夏季使用N46抗磨液压油,液压油过滤精度在5um左右,运行油温在20-50℃之间。在液压油初次使用前,应保证液压油经泵—过滤器—油箱—泵循环半小时以上,方可投伺服阀,避免液压油污染伺服阀。
2.1.2、阀位传感器
位移传感器是闭路电路控制系统中的重要元件,其性能的好坏直接影响到整个系统的控制精度和可靠性,现投用有外置滑片电阻式、电感式直线、角位移传感器和内置式电感式传感器等。它的作用是输出阀位反馈信号,反馈信号与输入信号经伺服放大器转换成电压信号并进行对比形成输出信号,控制执行机构的动作。传感器出现故障时,电液执行机构产生误动作直至系统锁位,阀动作的幅度视伺服放大器上阀位跟踪带宽和跟踪时间的设定值而定。
滑片电阻式传感器主要故障是在滑片与导电片接确处之间产生磨损,造成接确不良,输出信号跳跃,工作状态不稳定,这种形式的传感器故障较多,应进行改进否则投用可靠性低。外置式电感传感器其故障主要为电气紧固件松动、线圈质量问题或老化产生的故障,其运行故障较滑片电阻式传感器低。
内置式电感线圈传感器其传感器固定于油缸内,工作稳定性、可靠性能较高,运行中出现问题主要是密封件泄漏,液压油泄漏到电阻内,造成接确电阻增加,使阀位反馈信号产生偏差可中断,使其不能正常工作。
2.1.3、伺服油缸
伺服油缸首先要保证缸体耐压强度高,其次是保证缸筒与活塞之间极小的间隙和导向套适应小间隙,保证活塞密封环的可靠性。
运行中出现的主要问题是活塞密封环老化损坏,导致两油缸串油,虽故障出现几率较低,但依据故障现象较难判断故障原因。由于蝶阀和滑阀伺服油缸的结构和密封环不同,故障的现象也存在较大差异。滑阀油缸的活塞杆是双侧存在,蝶阀油缸的活塞杆是单侧存在,当调节信号给出(开/关)时,活塞先往调节方向运动,而后由于油缸活塞密封环老化损坏两油缸串油导通,导致油缸两侧油压平衡,滑阀活塞两侧面积相同,导致滑阀不动作;而蝶阀活塞面积不同(活塞杆是单侧存在),无活塞杆侧承受压强较大,导致阀向有活塞杆侧运动,直至蝶阀锁位油缸两侧进油停止,蝶阀运行位置由锁位设定的跟踪带宽、跟踪时间而定。所以当活塞密封环老化损坏后,滑阀的故障现象是先向调节方向运行后停止不动;蝶阀的故障现象是先向调节方向运行后向有活塞杆侧运行,直至锁位电磁阀动作锁位,油缸两侧达到平衡位置而停止运动。
2.1.4、其它液压件(油泵、电磁换向阀)
液压泵是液压系统的重要动力元件,它的质量好坏直接影响到液压控制系统的可靠性,早期使用较多的是国产叶片泵,其油压不稳定、油封泄漏、调节范围窄、工作噪音大,给使用、维护带来极大不利,后改用进口变量柱塞泵,其排量的调节是依靠压力补偿进行的,因此输出压力平稳,具有性能可靠、噪音低、运行周期长的特点。电磁换向阀是控制机构中大量存在的元件,其出现故障的频率较多(尤其是锁位电磁换向阀),主要故障是阀蕊卡死,原因是由于油质污染和在流动死区的沉积,使液压油经电磁换向阀向油缸供油,造成阀的误动作。此故障的检查较易,泄掉油系统压力后打开伺服机构,手按动电磁换向阀的两侧检查回弹性,如不能正常回弹证明电磁换向阀堵塞,解体清理后回装即可。
2.2、电气仪表系统的故障
随着仪表元件的技术不断提高,早期仪表元件耐低温能力差、工作稳定性较差,现阶段无论是兰州石化机械厂生产的电液执行机构还是九江仪表厂生产的产品,伺服放大器质量都比较过关。
3、电液执行机构在机组静叶调节系统上的应用
3.1、工作原理
由于电液执行机构的使用稳定性高,调节灵活使其应用范围扩大,现国内轴流风机静叶调节系统也相继采用了电液执行机构,主要工作方式为:电液伺服控制油路和电磁调节油路并联使用,通过静叶自动/静叶锁位的切换,执行两种工作状态。静叶伺服控制系统液压保护装置通过液压锁紧方式,控制电液伺服阀的进出油路和负载油路,当轴流风机处于正常状态时,液压锁电磁换向阀处于导通状态,电液伺服控制系统随调节器信号及负载情况及时调节静叶角度,达到适当风量。当由于非常原因(伺服控制系统中某控制元件发生故障,或其它干扰因素)使静叶角度与设定值偏差较大或完全失控时,锁位电磁阀换向阀上电通电,使液压锁处于关闭状态,切断电液伺服阀进出油路和负载油路,即时将静叶就地锁定。这时如果静叶角度与所要求的位置偏差较大,可以启动另一电磁换向阀调节,以点动方式对静叶角度进行修正,控制伺服油缸左、右移动,使静叶角度增大或减小,达到指定的位置。以使静叶不会完全失控,可以继续维持轴流风机工作。
3.2、本系统的缺点
由于考虑到安全运行的要求静叶角度25℃和紧急停车要求静叶保位(一般在60℃左右),在电液执行机构中有信号丢失、反馈信号丢失锁位,无信号偏差锁位功能,当因故障静叶角度发生较大的变化时无锁位功能,只能人为调整控制锁位,使本系统的安全性存在隐患,这是本系统的致命缺陷,这就要示电液执行机构尤其是伺服阀的可靠性极高,整个系统的工作稳定性要保证。
改进方案可结合滑阀、蝶阀控制系统,增上锁位电磁阀,在反馈信号与输入信号偏差较大时进行锁位,在投自保时自动解锁并控制阀位到相应位置。
4、电液执行机构使用几点意见
4.1、关于电液执行机构在故障断电状态下锁位电磁阀工作方式的选择问题
由于滑阀、蝶阀在催化装置中的重要作用不言而喻,因此在故障状态下执行机构的安全性能是非常重要的,要考虑到断电情况下阀的动作情况,一般来说锁位电磁换向阀为上电解锁,掉电锁位,保证在故障断电情况下保持阀位避免对生产产生较大影响,但这就对电磁阀的上电工作性能要求较高,要使用可靠性高电磁换向阀。
4.2、UPS电源的应用
为防止断电故障后阀误动作和不可调的状态,如有条件应增上UPS电源为仪表控制系统提供电源,确保在系统停电的故障状态下,利用蓄能器的油压控制阀位达到安全位置。
4.3、维护方便性
正常时伺服放大器面板上显示10个参数,主要为电源电压、伺服阀工作电压、偏差信号等,九江仪表厂在显示面板增上锁位电磁阀的工作状态(灯亮上电解锁/灯灭掉电锁位),对于操作人员的操作和维护带来极大便利,对于故障判断增加了手段。
4.4、关于电液执行机构关键电气仪表控制板卡的更换
随着装置运行周期不断延长,对设备的可靠性、稳定性及检修过程中的平稳性要求更高,由于伺服放大器上的仪表控制板卡尤其是主放大板和反馈板在装置开工前相应参数调校完毕,并进行全行程调试合格,如果正常生产中发生故障需要更换,重新调试的可能性非常小,即使可以调整参数但准确性非常低,而且不能进行全行程调试,因此建议在装置停工调试时对关键特阀准备二块相同的板卡,调试后一用一备,确保故障后平稳更换投用。
4.5、自保状态的调节方式
电液执行机构在自保状态下的工作方式,主要由通过电磁换向阀调节、电液伺服阀或两者同时动作调节方式。其中两者同时动作调节方式更为可靠,一方面动作速度快,另一方面确保在某一元件发生故障时也能保证自保动作正常。
4.6、电液执行机构的日常调节
有的装置特阀如烟机入口蝶阀或主旁路双动滑阀,长期处于一个位置,一方面传感器地此位置易卡,另一方面油缸油循环不流畅,易发生元件堵塞现象,应对执行机构进行经常性的小范围图调整,保证整个系统的正常运行。
5、执行机构的发展
随着计算机技术日趋完善和广泛应用,利用微机对电-液系统进行控制已成为机械行业实现机电一体化的一种重要手段,数字控制在当前被认为是实现对液压系统高速,高精度控制的最理想的方法之一。
5.1、数字式智能型执行机构
隨着可编程控制器和PLC控制系统的大量应用,以可编程控制器或PLC做主控制器的执行机构出现并投用,其工作特点如下:
(1)参数调节与整定信号通过数字写入方式,输入、输出和中央处理部分完全隔离,全数字控制,解决了原模拟信号受环境及电磁干扰的问题,工作稳定性得到较大提高。
(2)跟踪失调是依据分析信号变化和阀位的运动趋势而动作,使自锁动作更加准确,起到了真正的锁位保护作用,提高了整个系统的可靠性。
(3)增加了伺服阀的自动调校功能,使其工作稳定性得到较大提高。
(4)故障显示准确,基本做到了每个故障对应相应故障代码,使故障判断准确性提高。
5.2、液压缸的数字控制设计
数字阀可直接与微机接口而无需D/A转换装置,与单纯的伺服阀和比例阀相比,具有结构简单,工艺性好,成本低,抗污染性强,重复性能好,工作稳定可靠,能耗小等优点,因而在自动控制系统中独树一帜。
从流体控制的观点分,可分为连续流体控制和脉冲流体控制两种,在连续流体控制中,将运算处理的数字信号,经D/A转换为电气或机械信号,经过模拟式动作通过阀来控制流量。例如,由线性放大器驱动伺服阀和比例阀。
另一方面,脉冲流体控制是通过与位移信号相对应的一组脉冲信号直接使阀作断-通动作,形成间断的脉冲流体,从而达到控制平均流量输出的目的。
用2个高速阀控制受压面积不同的单杆式液压缸(图1)。阀V1和V2为常闭状态,液压缸不动。当V1或V2通电时,阀被打开,液压缸将向右或向左移动,其移动速度的控制是根据目标位置与实际位置之差,用PWM信号控制流量来达到目的,差值减小,脉冲宽度变短从而减速。
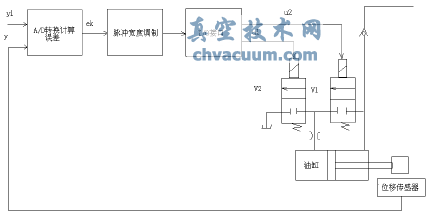
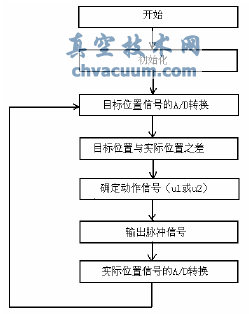
PWM控制位置程序的基本思路是:把目标位置信号r与实际位置y之差e作为模拟电信号,通过A/D转换器将数量化后的ek输入微机;乘上增益kp,计算出接通阀的脉宽时间(t=kpek),由此来确定通电时间;而根据ek的符号可判定应打开的阀(u1,u2)。为了提高控制缸位置的精度和稳定性,把死区宽度δ、使阀动作的最小脉冲宽度t1及计算时间t2均输入随机存取存储器。图是用PWM操纵的两个高速电磁阀控制液压缸的程序框图。
进入数字时代以后工程控制数字化已成为了必然的发展趋势,在电液控制技术领域应用数字阀实现直接数字控制是数字化的理想解决方案。拟开展的研究方向通过发展出新型的系列数字阀,并将其应用于电液控制系统,通过数字控制器对液压系统输出的动力参数实现直接数字控制,从而达到电液控制技术数字化的目的,并形成具有自主知识产权的、独特的电液数字伺服的控制方案。