结合CATIA-DMU Kinematics的车身运动件结构设计
结合CATIA-DMUKinematics的车身运动件结构设计能提升运动件产品的制造可靠性并缩短设计调试周期,从而达到高品质低成本的效益。本文介绍了此设计方法的基本步骤和关键点、难点,并通过车身上一运动件(加油口)的设计案例详细说明了其具体运用。
车身运动件较一般零部件设计还涉及到动态设计分析,其性能可靠性是影响整车性能的重要因素,如何实现低成本、高效率的运动件结
构设计、制造和生产对于整车开发至关重要。
结合CATIA- DMUKinematics 的车身运动件结构设计是以达到高品质低成本运动件产品为目的,基于在产品设计初期就综合分析运动件的整个开闭过程的思想,同时结合CATIA软件DMUKinematics 模块的数字化高效运动模拟,缩短设计分析周期。
1、基本步骤
随着科学技术的发展,车身设计方法进入了现代车身设计阶段,其流程一般包括产品规划、定义阶段,造型阶段,详细可行性分析阶段,详细工程设计阶段,设计验证阶段和制造阶段六个阶段,结合CATIA- DMUKinematics 的车身运动件结构设计的基本步骤有:
1) 竞争车型件对比研究和参数性能目标定义;
2) 结合CATIA- DMUKinematics 的运动件工程可行性分析的造型面设计;
3) 结合CATIA- DMUKinematics 进行运动件的详细可行性分析;
4) 运动件的详细工程设计,根据详细工程可行性分析,进行三维结构设计,同步进行结合CATIA- DMUKinematics 虚拟动态分析;
5) 运动件的设计验证,进行软工装样件制造和试验验证;
6) 运动件的制造,从小批量生产、产量爬坡,一直到满足批量生产节奏的要求,整个设计开发主体工作完成。
2、关键点及难点
在造型阶段,运用CATIA- DMUKinematics 进行运动件的动态分析,反馈造型面的工程可行性,从而改善调整造型面获得能满足运动件设计约束要求的最终造型面,在详细可行性分析阶段进行结合CATIA-DMUKinematics 的运动件动态分析能确定合理的运动件结构设计的详细方案,是进行运动件详细工程设计的基础条件和前提,也是实现运动件功能的关键。
在详细工程设计阶段运用CATIA- DMUKinematics 进行运动件的动态分析,能设计出可靠稳定的运动件产品结构,减少验证阶段和最终的制造阶段的修改和反复调试,缩短运动件产品的开发周期并降低成本,是整个设计的难点。
3、实例介绍
本文通过车身上的加油口总成运动件的设计阐述结合CATIA-DMUKinematics的车身运动件结构设计的运用。
3.1、产品规划、定义阶段
加油口总成在一般分为合页式和分体式(悬臂式) 两大类,可采用塑料和钣金材质。本加油口总成初步定义为钣金结构,内外板采用焊接,通过螺栓连接到白车身上。
3.2、造型阶段
基于造型面和分缝线可获得加油口外板和侧围外板草数据,DMU分析如图1 所示,可知:合页式结构随着开启角度的增大,运动间隙越小;分体式结构随着开启角度的增大,运动间隙增大;基于本CAS 面信息合页式结构不可行(开启28°后发生干涉),分体式结构04 和分体式结构05 均满足最小运动间隙均满足大于2mm 要求。可接受造型面进入下一阶段。
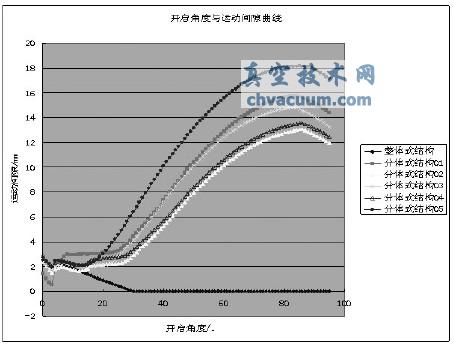
图1 造型阶段DMU 分析结果
3.3、详细可行性分析阶段
基于造型面阶段确定的方案进行结构的断面设计、主体方案分析和工艺可行性分析,再进行DMU分析。虽然分体式结构04 的最小运动间隙大于分体式结构05 的最小运动间隙,有更大的公差兼容性,但分体式结构05 较分体式结构04 开启角度与运动间隙曲线更平稳,稳定性更好,可靠性更高,故选定分体式结构05 方案进行详细设计阶段。
3.4、详细设计阶段
在详细设计阶段需进行内部结构的细节设计。分体式加油口总成结构中外板、加强板和铰链臂随铰链轴转动,加强板被外板包袱在内侧,故其对运动间隙的影响由外板结构决定;铰链臂的结构特征对运动间隙的影响则需进行DMU分析,保证整个加油口结构均能满足开启运动间隙。从分析可知,悬臂的宽度及其上的加强筋深度,两侧的翻边均会影响运动间隙,综合考虑悬臂的结构刚度通过DMU分析可获得最佳的悬臂宽度及加强筋深度和翻边高度、角度。从而获得最终的加油口详细设计数据。
3.5、试制验证阶段
完成加油口总成的样件试制并跟进试制反馈问题,进行加油口总成结构的优化和改善并对优化和改善后的结构进行DMU校核,满足校核则进入批量制造阶段,否则需重新制定优化和改善方案直至满足DMU校核。
3.6、批量制造阶段
完成加油口总成批量制造阶段工作,并跟进产品的最终状态反馈问题,进行问题解决。
4、总结
本文基于一般车身开发流程阐述了结合CATIA- DMUKinematics 的车身运动件结构设计基本步骤;此方法的关键在于造型阶段和详细可行性阶段,而难点在于产品详细工程设计阶段;加油口总成设计实例阐述了此方法在整个产品设计的具体应用;此设计适用于车身上运动件产品设计,能提高产品的稳定可靠性,减短产品开发周期和降低成本。