双活塞缸式气动真空发生器的改进设计及试验研究
双活塞缸式气动真空发生器相对于目前广泛使用的射流式真空发生器,它具有供给压力低、耗气量少的优点,在气动真空系统中具有很大的应用前景。文中针对原系统中设计的不足,提出了以一个抽气换向阀替代原有两个抽气单向阀的改进设计。试验研究结果表明,改进后系统的主要性能在原有基础上均有一定程度的提高,极限真空度可达93kPa,超过同级别的射流式真空发生器,在同样供给流量下,抽取1L容器真空度达80kPa时的响应时间减少了12.5%。
在工业自动化发展过程中,气动真空吸取技术已越来越广泛地应用于各种生产线上,主要用于吸取易碎、柔软、薄的非铁、非金属材料,以完成搬运、夹紧或包装等作业。目前,在生产线上广泛应用的真空发生装置主要为射流式真空发生器,压缩气体通过喷嘴的高速流动从而产生一定的真空度。根据其工作原理决定了它只能在较高的供给压力下才能达到极限真空度,并且耗气量大,不利于气动系统节能。真空技术网(http://www.chvacuum.com/)前文中提出了一种新型的真空发生器PVSCTC-1(Pneumatic Vacuum System Consisting of Two Cylinders-1),工作原理如图1所示,它可在相对较低的供给压力下达到较高的极限真空度,这就有可能直接或接利用气缸排气的能量进行工作,产生真空,达到气动系统节能的目的,在工程应用中具有较高的应用价值。
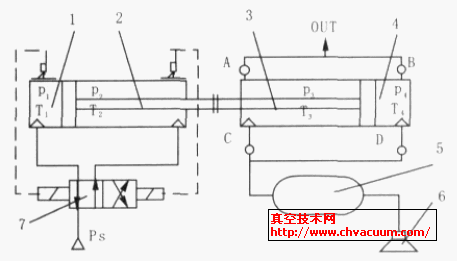
1.动力腔Ⅰ 2.动力腔Ⅱ 3.真空腔Ⅰ 4.真空腔Ⅱ 5.连接管道等效容器 6.真空吸盘 7.换向阀
图1 双活塞缸式气动真空发生器工作原理
这种新型的真空发生器作为一种节能的气动真空发生装置,在满足基本性能要求的基础上,本身应具有较高的能量使用效率,否则研究意义不大。通过前期的研究发现,其响应时间和耗气量这两个性能指标上较同级别的射流式真空发生器都还存在一定的差距。本文研究的目的正是通过相关的理论分析,对其不足之处进行改进,提高整体能力水平。
1、改进设计的理论依据
1.1、极限真空度分析
系统的工作原理在真空技术网另文中已叙述,当真空腔室无法继续抽取等效真空容器中的气体时,即真空腔室余隙容积中的气体完全膨胀后的压力恰等于真空容器中的气体压力与抽气单向阀开启压力之和时,达到了系统的极限状态,真空容器达到极限真空度。根据绝热过程的气体状态方程可得,系统达到极限状态时真空腔室内与真空容器(真空吸盘)所能达到的极限真空度p'vmax、pvmax分别为:
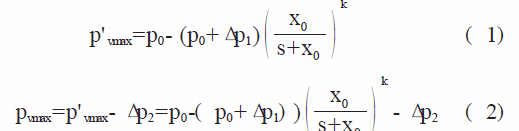
式中p0———大气压力,Pa
Δp1———排气单向阀开启压力,Pa
Δp2———抽气单向阀开启压力,Pa
s———活塞运动行程,m
x0———真空腔室余隙容积等效行程,m
由式(1)和式(2)可知,真空容器内的极限真空度与抽、排气单向阀的开启压力、腔体余隙容积和行程大小都相关,并且低于真空腔室内的极限真空度,差值为抽气单向阀开启压力大小,并且抽气单项阀的开启压力对吸盘处所能达到的真空度影响最为直接。例如,单向排气阀、吸气阀开启压力为12kPa时,若真空腔室内能够达到的最高真空度为95kPa,则真空吸盘处能达到的最大真空度约为83kPa。由此说明,在抽气过程中,其中有很大一部分的压力损失在抽气单向阀处。
1.2、响应时间分析
系统响应时间是与系统的有效抽速和被抽取容器容积大小相关的,关系如下:

式中pc———等效真空容器内气体绝对压力,Pa
V———等效真空容器容积,L
Se———系统有效抽速,L/min
在特定的工作场合下,被抽取的容器大小或连接的管道长度一般都是固定的。因而,系统的有效抽速得到了提高,系统响应时间也就响应减少了。而系统的有效抽速是由真空发生装置的自身抽速和抽气流道的流通性能共同决定的,在一定的供给流量下,其自身的抽速是确定的。只能通过提高抽气流道的流通性能来减少系统响应时间。
随着真空容器内的真空度逐渐升高,真空腔室与真空容器间的压差逐渐减小,每个抽气过程抽气单向阀的开启程度也相应减小,使得真空腔室更加难以从真空容器内抽出气体,最终导致系统响应时间增加。所以,抽气单向阀对抽气流道的流通性能以及系统有效抽速都有较大的影响,不利于减少系统响应时间。
综上所述,图1中的两个抽气单向阀不仅影响了系统极限真空度,而且在抽气过程中,尤是当入口真空度较高时,其开启程度的减小也限制了系统响应时间的减少,需要对系统结构进行相应改进,提高双活塞缸式气动真空发生器的性能水平。
2、系统结构改进设计
上节中通过对系统极限真空度和响应时间的分析,发现了现阶段限制系统主要性能提高的主要原因。因此,本文提出了采用一个抽气换向阀来替代原有两个抽气单向阀的改进设计,改进后的系统工作原理如图2所示,命名为PVSCTC-2。
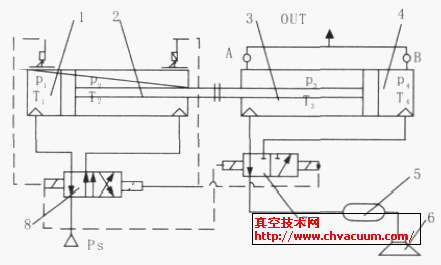
1.动力腔Ⅰ 2.动力腔Ⅱ 3.真空腔Ⅰ 4.真空腔Ⅱ 5.真空容器 6.真空吸盘 7.抽气换向阀 8.驱动换向阀
图2改进后的真空发生器系统工作原理
活塞式真空发生器的抽气过程采用抽气换向阀控制时,不仅消除了抽气流道中原抽气单向阀开启压力的损失,也克服了抽气过程抽气有效面积逐渐减小的不利影响,有利于提高系统极限真空度、减少响应时间。但在PVSCTC-2型中依然保留了原两个排气单向阀,这是因为若同样以换向阀取代两排气单向阀,虽然可使真空腔排气时余隙容积气体压力有所降低,也减少了回流气体产生的真空压力波动,但当活塞反向运动时,大气气体也将流入上一次行程中的抽气腔内,反而增加了活塞运动时的阻力,不利于往复运动速度的提高,从而也影响系统的有效抽速;另外,若突然停止气源供气,活塞很可能最终停留在行程的一侧,使抽气换向阀处在换向过程中,这样就不能保证真空腔室与真空容器连接的密闭性,不能维持住真空吸盘处原有的真空度,导致吸取的工件脱落。所以,为了避免上述两点不利影响,保留了原有两个排气单向阀。
但是,在此改进的同时,也随之带来了不利的影响。由于在具体结构设计时,抽气换向阀是位于动力腔室和真空腔室之间,靠外侧的真空腔室Ⅱ在抽气时需绕过整个真空腔体,不可避免使得余隙容积增大,这对系统极限真空度有不利影响,也增大了真空容器中压力波动。
在具体零部件结构设计前,先对系统进行了仿真研究,主要参数如下:动力腔直径40mm,真空腔直径40mm,活塞杆直径8mm,行程40mm,供给压力0.15MPa。图3为系统结构改进前后的真空响应过程对比。仿真结果表明,PVSCTC-2在系统极限真空度和响应时间这两项主要性能标上都有一定程度提高。同时,图3中PVSCTC-2的真空响应过程也的确出现之前分析的气体回流产生的真空度波动现象,这是由结构设计所造成的,无法避免,只能通过尽可能减小真空腔室的余隙容积来减小波动。
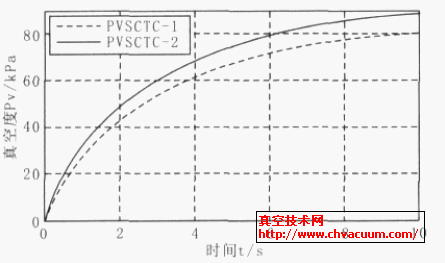

图3 系统改进前后真空响应过程仿真结果对比 图4 在相同结构参数下真空响应过程实验对比
3、试验研究
3.1、试验验证
通过系统的仿真研究,表明采用一抽气换向阀替代原有的两个抽气单向阀能够使系统性能得到一定程度的提高,改进是可行的,但还需通过试验研究的方法来进行验证。本文根据图2所示的系统工作原理设计了改进后样机模型的各具体零部件结构,并进行了相关的试验研究。图4为PVSCTC-1、PVSCTC-2样机模型在相同结构参数下,供给压力为0.15MPa时实验测得的真空响应过程对比,模型结构参数见上节。从图中可看出,改进后的PVSCTC-2样机模型较PVSCTC-1在极限真空度和响应速度上都有较大幅度的提高,尤其是达到较高真空度时的响应时间大大减少了。而在相同的供给压力下,两者的供给流量几乎相同,这说明了在相同供给耗气量的情况下,改进后模型的实际有效抽气流量比原模型的大,抽气效率更高,与之前的理论分析和仿真结果是一致的。图4在相同结构参数下真空响应过程实验对比
3.2、主要影响因素试验研究
(1)动力腔直径的影响
通过对多组不同动力腔直径下的样机模型进行试验,结果表明,动力腔直径与系统的极限真空度基本无关,主要是对活塞的往复运动速度有较大的影响,从而影响系统在不同入口真空度下的实际抽速,即流量特性。图5为不同动力腔直径下,PVSCTC-2样机模型在相同供给压力下试验测得的系统流量特性。在一定范围内动力腔直径越小,活塞往复运动速度也越快,实际有效抽速越高。这是因为,越大的驱动直径进、排气体的质量也越多,在相同进、排气流道有效面积下,需要的时间也越长,使得活塞的运动速度降低,最终导致有效抽速的下降。
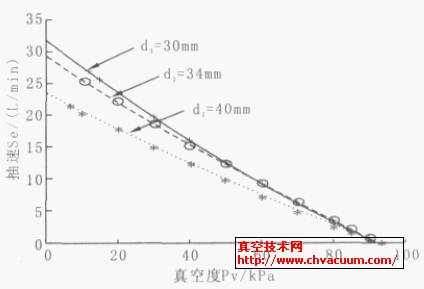
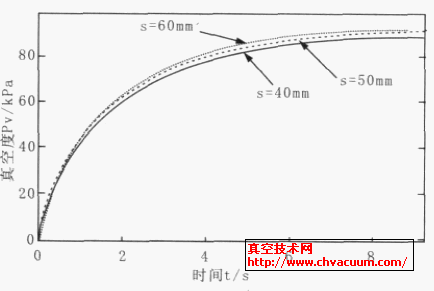
图5 不同驱动腔直径下的流量特性 图6 不同行程下的真空响应过程对比
(2)行程的影响
由式(1)可知,行程是影响其极限真空度的主要因素之一,行程越大,系统所能获得的极限真空度也越高。但是,行程大小同时也决定总体结构轴向尺寸的大小,外形尺寸与性能是相矛盾的。通过实验,测得了不同行程下真空响应过程,如图6所示。活塞运动行程分别为40mm、50mm、60mm时,系统所能达到的极限真空度分别约为93kPa、92kPa、89kPa。
从图6中还可看出,增加行程大小对系统响应时间的减少也是有利的,行程为60mm时的系统响应时间较行程为40mm时减少了16%。从实验测得的供给流量上看,不同行程下的供给流量基本是相同的,这就说明了行程为60mm时系统真空度达80kPa的总耗气量较行程40mm时也减少16%。所以,在外形尺寸限定范围内增大行程对提高系统极限真空度、减少系统响应时间和空气消耗量都是有利的。
(3)供给压力的影响
根据系统的工作原理,最低供给压力可由作用在活塞上的力平衡关系求得,在不同驱动腔与真空腔工作面积比下,最低供给压力大小也随之改变。以驱动腔直径30mm,真空腔直径40mm,极限真空度90kPa为例,计算得到最低供给压力约为0.21MPa,当供给压力高于最低值时都可进行抽取真空。所以,活塞式真空发生器可以在一个很宽的供给压力范围内达到极限真空度,而并非像射流式真空发生器只能在0.45MPa左右时才能达到极限真空度。
随着供给压力的提高,活塞式真空发生器的供给流量也随之增加,活塞往复运动速度加快,真空响应速度也有一定程度的提高,但是并不明显,如图7所示,而供给流量却大大增加了。所以,通过提高供给压力来减少系统响应时间是不合适的,应在满足响应时间要求的基础上尽可能降低供给压力,这样才符合气动系统节能的思想。
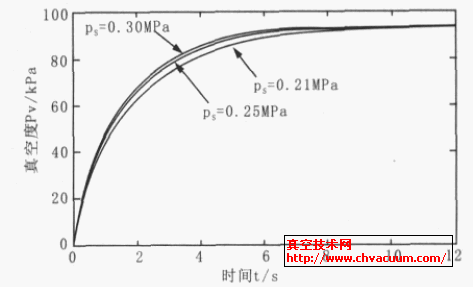
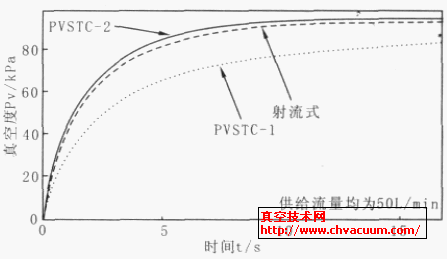
图7 不同供给压力下的真空响应过程对比 图8 在相同供给流量下(50L/min),各真空发生真空响应过程对比
3.3、与同级别射流式真空发生器对比
目前,本文研究活塞式真空发生器最大抽速在30L/min附近,以下将它与同级别射流式真空发生器的主要性能进行比较。图8为各真空发生器在相同供给流量下(50L/min),抽取1L真空容器的真空响应过程对比,主要数据见表1。其中PVSCTC-2样机模型的主要结构参数为:动力腔直径30mm,真空腔直径40mm,行程60mm。
表1 各真空发生器的主要性对比
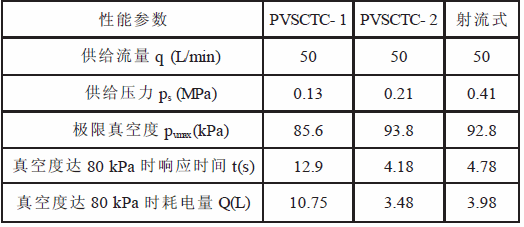
由上述各项性能对比可得,通过本文的研究,对PVSCTC-1进行改进后得到的PVSCTC-2样机模型的极限真空度和响应时间这两个主要性能指标在原有基础上都有不同程度地提高,甚至超过了同级别的射流式真空发生器。在相同使用的情况下,改进后的样机模型更加节省耗气量,真空度达80kPa时的耗气量减少了约12.5%,同时供给压力更低,达到了本文的研究目的。
4、结论
针对前文中设计的双活塞缸式气动真空发生器的性能不足,本文从理论上对系统极限真空度和响应时间的主要影响因素进行了分析,发现PVSCTC-1系统中的两个抽气单向阀是现阶段限制其系统性能提高的主要因素,为此提出了以一个抽气换向阀替代原两个抽气单向阀的改进设计,并通过试验研究对系统改进进行了验证。文中还分析了系统主要结构参数和工作参数对其主要性能的影响。通过与同级别的射流式真空发生器的主要性能对比,结果表明,在相同供给流量下,本文研究的PVSCTC-2原型样机模型较同级别的射流式真空发生器达相同真空度时的耗气量减少了约12.5%,供给压力更低,有利于气动系统节能。